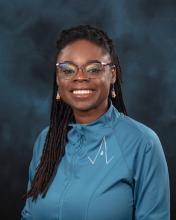
Bianca Bailey
Agriwater Corporation
Bio:Bianca Bailey is the founder of Agriwater, a company dedicated to developing a mobile wastewater treatment system that transforms livestock manure into clean water and organic fertilizer. This…
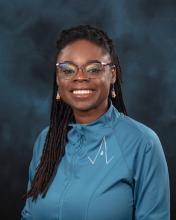
Bianca Bailey
Agriwater, Founder & CEO
Bio:
Bianca Bailey is the founder of Agriwater, a company dedicated to developing a mobile wastewater treatment system that transforms livestock manure into clean water and organic fertilizer. This cutting-edge technology not only purifies animal waste but also reduces greenhouse gas emissions and creates additional revenue streams for farmers. Agriwater provides an essential environmental compliance solution, helping farmers avoid costly fines for manure pit or lagoon spills into rivers.
Bianca holds a Ph.D. in Agricultural and Biological Engineering and an M.S. in Environmental Engineering from the University of Illinois Urbana-Champaign, as well as a B.S. in Chemical Engineering from Howard University. She is also an alumna of the GEM Fellowship program.
Project Abstract:
Agriwater is revolutionizing sustainable water management with its innovative mobile water treatment systems, designed to transform livestock manure water into valuable by-products: clean water, organic fertilizer, and carbon credits. Through extensive research and customer feedback, Agriwater identified a critical challenge faced by livestock farmers: the environmental compliance issues related to the leaching of toxic animal manure from lagoons and storage pits. These issues can lead to costly environmental violation fines, plant shutdowns, and even imprisonment due to non-compliance with the National Pollutant Discharge Elimination System (NPDES) regulations.
Agriwater’s advanced technology not only addresses these compliance concerns but also provides farmers with commercially viable solutions that contribute to environmental sustainability and economic efficiency.
Bio:
Bianca Bailey is the founder of Agriwater, a company dedicated to developing a mobile wastewater treatment system that transforms livestock manure into clean water and organic fertilizer. This cutting-edge technology not only purifies animal waste but also reduces greenhouse gas emissions and creates additional revenue streams for farmers. Agriwater provides an essential environmental compliance solution, helping farmers avoid costly fines for manure pit or lagoon spills into rivers.
Bianca holds a Ph.D. in Agricultural and Biological Engineering and an M.S. in Environmental Engineering from the University of Illinois Urbana-Champaign, as well as a B.S. in Chemical Engineering from Howard University. She is also an alumna of the GEM Fellowship program.
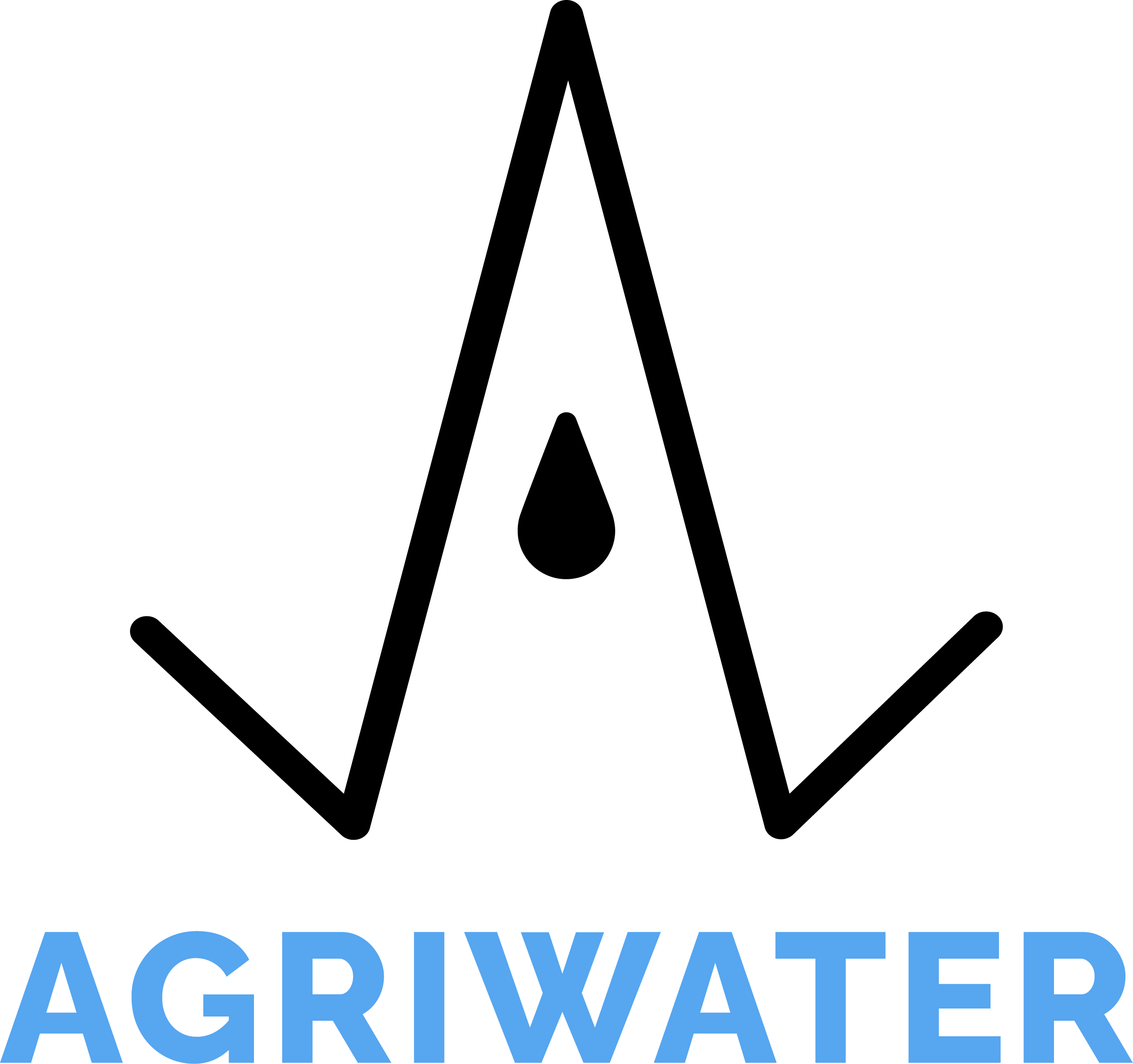
Project Abstract:
Agriwater is revolutionizing sustainable water management with its innovative mobile water treatment systems, designed to transform livestock manure water into valuable by-products: clean water, organic fertilizer, and carbon credits. Through extensive research and customer feedback, Agriwater identified a critical challenge faced by livestock farmers: the environmental compliance issues related to the leaching of toxic animal manure from lagoons and storage pits. These issues can lead to costly environmental violation fines, plant shutdowns, and even imprisonment due to non-compliance with the National Pollutant Discharge Elimination System (NPDES) regulations.
Agriwater’s advanced technology not only addresses these compliance concerns but also provides farmers with commercially viable solutions that contribute to environmental sustainability and economic efficiency.
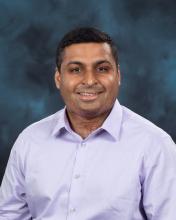
Rajan Kumar
Ateios Systems
Bio:Rajan Kumar, PhD, is a National Science Foundation Graduate Research Fellow and a Forbes Next 1000 Fellow with over 11 years of expertise in nanoscale research and the commercialization of deep…
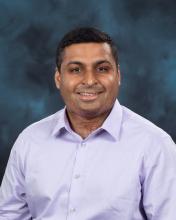
Rajan Kumar
Ateios Systems, CEO
Bio:
Rajan Kumar, PhD, is a National Science Foundation Graduate Research Fellow and a Forbes Next 1000 Fellow with over 11 years of expertise in nanoscale research and the commercialization of deep technology. He stands out as one of the few doctoral engineers with a specialized focus in nanoengineering, having studied at two of the world's leading institutions: the State University of New York (SUNY) at Albany (now SUNY Polytechnic) and the University of California, San Diego (UCSD).
At UCSD, Rajan earned both his doctoral and master’s degrees in Nanoscale Engineering, concentrating on printed electronics and novel composites for electrochemical devices. His doctoral research led to the development and patenting of the world’s first printable stretchable battery, recognized as one of 13 battery innovations poised to change the world.
Drawing on his background in advanced materials and manufacturing, as well as expertise in analytical software, Rajan and his team at Ateios Systems are revolutionizing the design, engineering, and manufacturing of batteries.
Project Abstract:
Ateios Systems is at the forefront of developing breakthrough coating and processing technologies essential for scaling solid-state batteries (SSBs) through rapid heterogeneous deposition methods. Our key innovation is the use of radiation-curable composite electrodes, which significantly enhance battery energy density by over 350 Wh/kg while reducing costs to under $100/kWh. These composites enable a tenfold increase in manufacturing speed (up to 940 m²/min), lower processing costs by more than 20%, and eliminate the need for toxic organic solvents, offering a positive environmental impact.
The radiation-curable composites are applied using roll-to-roll coating systems such as comma bar or slot-die, and are combined with solid-state electrolytes to develop a heterogeneous deposition processing system that precisely controls microstructure, interfaces, and form factors.
This project represents a critical step towards creating widespread, safe, and high-energy dense SSBs. It also aims to revitalize American battery manufacturing, addressing the current challenge where only 1% of lithium-ion batteries are produced in the U.S., posing security, environmental, and economic risks. By utilizing radiation-curable composite electrodes and water-in-salt electrolytes, Ateios Systems will overcome these challenges and establish a U.S.-based manufacturing capability capable of producing 20 TWh of clean storage by 2030 in just 2 years, compared to 30 years using traditional methods.
Bio:
Rajan Kumar, PhD, is a National Science Foundation Graduate Research Fellow and a Forbes Next 1000 Fellow with over 11 years of expertise in nanoscale research and the commercialization of deep technology. He stands out as one of the few doctoral engineers with a specialized focus in nanoengineering, having studied at two of the world's leading institutions: the State University of New York (SUNY) at Albany (now SUNY Polytechnic) and the University of California, San Diego (UCSD).
At UCSD, Rajan earned both his doctoral and master’s degrees in Nanoscale Engineering, concentrating on printed electronics and novel composites for electrochemical devices. His doctoral research led to the development and patenting of the world’s first printable stretchable battery, recognized as one of 13 battery innovations poised to change the world.
Drawing on his background in advanced materials and manufacturing, as well as expertise in analytical software, Rajan and his team at Ateios Systems are revolutionizing the design, engineering, and manufacturing of batteries.
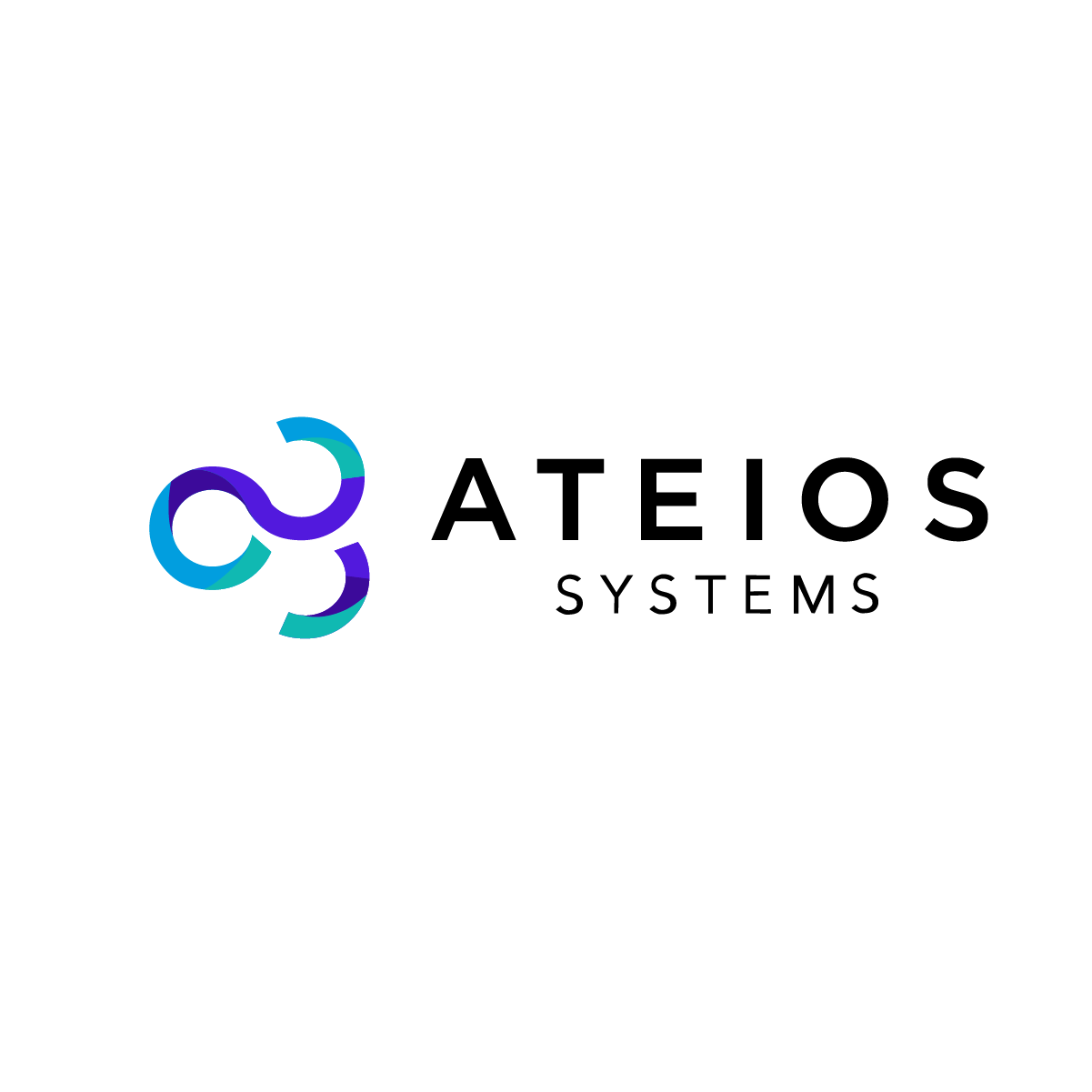
Project Abstract:
Ateios Systems is at the forefront of developing breakthrough coating and processing technologies essential for scaling solid-state batteries (SSBs) through rapid heterogeneous deposition methods. Our key innovation is the use of radiation-curable composite electrodes, which significantly enhance battery energy density by over 350 Wh/kg while reducing costs to under $100/kWh. These composites enable a tenfold increase in manufacturing speed (up to 940 m²/min), lower processing costs by more than 20%, and eliminate the need for toxic organic solvents, offering a positive environmental impact.
The radiation-curable composites are applied using roll-to-roll coating systems such as comma bar or slot-die, and are combined with solid-state electrolytes to develop a heterogeneous deposition processing system that precisely controls microstructure, interfaces, and form factors.
This project represents a critical step towards creating widespread, safe, and high-energy dense SSBs. It also aims to revitalize American battery manufacturing, addressing the current challenge where only 1% of lithium-ion batteries are produced in the U.S., posing security, environmental, and economic risks. By utilizing radiation-curable composite electrodes and water-in-salt electrolytes, Ateios Systems will overcome these challenges and establish a U.S.-based manufacturing capability capable of producing 20 TWh of clean storage by 2030 in just 2 years, compared to 30 years using traditional methods.
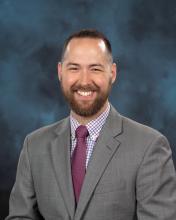
Alex Stiles
Vitriform3D Incorporated
Bio:Alex Stiles holds a Bachelor's degree in Mechanical Engineering from the Illinois Institute of Technology and a Ph.D. in Energy Science and Engineering from the University of Tennessee, Knoxville…
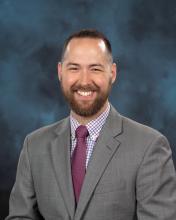
Alex Stiles
Vitriform3D, Co-founder & CEO
Bio:
Alex Stiles holds a Bachelor's degree in Mechanical Engineering from the Illinois Institute of Technology and a Ph.D. in Energy Science and Engineering from the University of Tennessee, Knoxville. During his undergraduate studies, Alex founded Samambu LLC, a bamboo fiber composites company that garnered awards at three business plan competitions.
Following his undergraduate studies, Alex worked as a product engineer in the railroad industry for nearly four years before pursuing graduate research in advanced composites and additive manufacturing (AM). Under the guidance of Dr. Uday Vaidya, his dissertation focused on photopolymer formulation and cure kinetics for large-scale AM. With over a decade of experience in polymeric composites and tooling, Alex brings extensive expertise to his work in the field.
Project Abstract:
Vitriform3D is transforming the 3D printing landscape by utilizing recycled glass as a feedstock in powder bed 3D printing technology. Despite being infinitely recyclable, over 8 million tons of glass in the U.S. end up in landfills each year due to its low raw material value. Vitriform3D's patent-pending Binder Jet Technology (BJT) addresses this issue by enabling the use of recycled glass in large-scale 3D printing applications.
Our innovative technology capitalizes on glass’s inherent wear resistance and optical properties to produce durable glass composite products with high resolution and virtually unlimited design possibilities. Our initial focus is on tooling for the marine industry, where large-scale BJT can significantly reduce production time and manual labor requirements. By being based in the Oak Ridge/Knoxville area, Vitriform3D is strategically positioned to engage with the marine tooling industry and obtain valuable feedback for further development of our technology.
Bio:
Alex Stiles holds a Bachelor's degree in Mechanical Engineering from the Illinois Institute of Technology and a Ph.D. in Energy Science and Engineering from the University of Tennessee, Knoxville. During his undergraduate studies, Alex founded Samambu LLC, a bamboo fiber composites company that garnered awards at three business plan competitions.
Following his undergraduate studies, Alex worked as a product engineer in the railroad industry for nearly four years before pursuing graduate research in advanced composites and additive manufacturing (AM). Under the guidance of Dr. Uday Vaidya, his dissertation focused on photopolymer formulation and cure kinetics for large-scale AM. With over a decade of experience in polymeric composites and tooling, Alex brings extensive expertise to his work in the field.
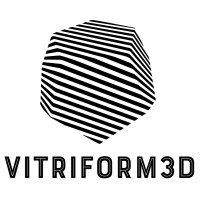
Project Abstract:
Vitriform3D is transforming the 3D printing landscape by utilizing recycled glass as a feedstock in powder bed 3D printing technology. Despite being infinitely recyclable, over 8 million tons of glass in the U.S. end up in landfills each year due to its low raw material value. Vitriform3D's patent-pending Binder Jet Technology (BJT) addresses this issue by enabling the use of recycled glass in large-scale 3D printing applications.
Our innovative technology capitalizes on glass’s inherent wear resistance and optical properties to produce durable glass composite products with high resolution and virtually unlimited design possibilities. Our initial focus is on tooling for the marine industry, where large-scale BJT can significantly reduce production time and manual labor requirements. By being based in the Oak Ridge/Knoxville area, Vitriform3D is strategically positioned to engage with the marine tooling industry and obtain valuable feedback for further development of our technology.
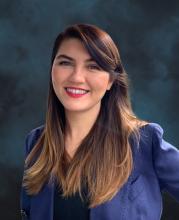
Anca Timofte
Holocene Climate Corporation
Bio:Anca Timofte earned her B.S. in Chemical Engineering from Washington University in St. Louis, where she also served as a research fellow in the Environmental NanoChemistry Laboratory. She pursued…
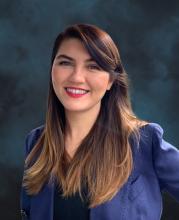
Anca Timofte
Holocene Climate Corporation, Co-founder & CEO
Bio:
Anca Timofte earned her B.S. in Chemical Engineering from Washington University in St. Louis, where she also served as a research fellow in the Environmental NanoChemistry Laboratory. She pursued her interest in environmental applications by obtaining an M.S. in Environmental Engineering from ETH Zurich.
Anca spent seven years at Climeworks, developing and implementing chemical processes for direct-air-capture plants. As a process engineering team lead, she managed the design and engineering of over 14 carbon removal plants and built a skilled team.
In June 2022, Anca completed her MBA at the Stanford Graduate School of Business, focusing on the intersection of climate and finance. As the Founder and CEO of Holocene, she is dedicated to pioneering innovative carbon removal solutions.
Project Abstract:
Holocene specializes in designing and building chemical plants that efficiently extract carbon dioxide (CO2) from the atmosphere using a groundbreaking organic chemistry developed and tested at ORNL. The process involves two organic compounds working in tandem: one compound enhances water’s capacity to absorb CO2, while the other facilitates the removal of CO2 from the water by forming a solid precipitate. When this solid is heated, the CO2 is released in a concentrated form, ready for permanent underground storage.
This process generates negative emissions—an environmental benefit akin to carbon credits. Companies and institutions with net-zero carbon commitments are already purchasing negative emissions to meet their sustainability goals. Additionally, both the European Union and the U.S. governments are fostering the development of negative emissions technologies through financial incentives, such as the Low Carbon Fuel Standard and the 45Q tax credit. Holocene aims to provide negative emissions solutions to corporations and governments, supporting their efforts to achieve decarbonization targets.
Bio:
Anca Timofte earned her B.S. in Chemical Engineering from Washington University in St. Louis, where she also served as a research fellow in the Environmental NanoChemistry Laboratory. She pursued her interest in environmental applications by obtaining an M.S. in Environmental Engineering from ETH Zurich.
Anca spent seven years at Climeworks, developing and implementing chemical processes for direct-air-capture plants. As a process engineering team lead, she managed the design and engineering of over 14 carbon removal plants and built a skilled team.
In June 2022, Anca completed her MBA at the Stanford Graduate School of Business, focusing on the intersection of climate and finance. As the Founder and CEO of Holocene, she is dedicated to pioneering innovative carbon removal solutions.
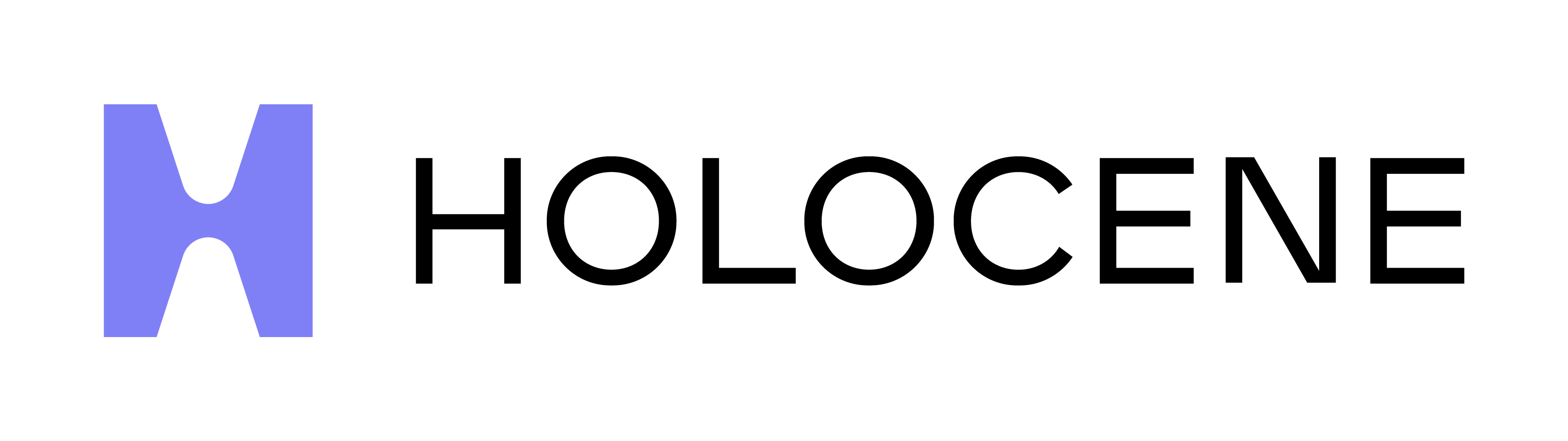
Project Abstract:
Holocene specializes in designing and building chemical plants that efficiently extract carbon dioxide (CO2) from the atmosphere using a groundbreaking organic chemistry developed and tested at ORNL. The process involves two organic compounds working in tandem: one compound enhances water’s capacity to absorb CO2, while the other facilitates the removal of CO2 from the water by forming a solid precipitate. When this solid is heated, the CO2 is released in a concentrated form, ready for permanent underground storage.
This process generates negative emissions—an environmental benefit akin to carbon credits. Companies and institutions with net-zero carbon commitments are already purchasing negative emissions to meet their sustainability goals. Additionally, both the European Union and the U.S. governments are fostering the development of negative emissions technologies through financial incentives, such as the Low Carbon Fuel Standard and the 45Q tax credit. Holocene aims to provide negative emissions solutions to corporations and governments, supporting their efforts to achieve decarbonization targets.
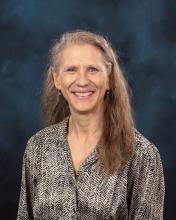
Kim Tutin
Captis Aire LLC
Bio:Kim Tutin is the visionary Founder and CEO of Captis Aire, a company dedicated to commercializing the Fluidized Bed Concentrator (FBC), an advanced air pollution control technology tailored for…
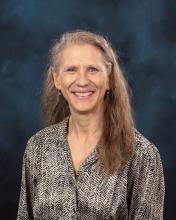
Kim Tutin
Captis Aire, Founder & CEO
Bio:
Kim Tutin is the visionary Founder and CEO of Captis Aire, a company dedicated to commercializing the Fluidized Bed Concentrator (FBC), an advanced air pollution control technology tailored for the wood products industry. Under Kim's passionate and strong leadership, her team has achieved significant milestones, including:
- Successfully completing two pilot runs of the FBC at a commercial wood products manufacturing site.
- Securing a $5 million letter of intent from an FBC customer.
- Acquiring a technology license for the FBC.
As the inventor of the FBC, Kim played a crucial role in filing and defending two patent applications for the technology. Before founding Captis Aire, she held various positions at Georgia-Pacific Chemicals, including chemist, group leader, and technology scout, where she was instrumental in developing new technologies.
Kim holds a bachelor’s degree in Chemistry from the University of Minnesota and an MBA in Technology and Engineering Management from the City University of Seattle.
Project Abstract:
As global efforts intensify to reduce air pollutants, Captis Aire is at the forefront with a cutting-edge technology designed to capture air pollutants from wood products manufacturing sites. These sites include producers of liquid biofuels, wood pellets, oriented strand board, plywood, and lumber. A key pollutant released during the wood drying process is turpentine, which is valuable and can be repurposed for various uses, including as biofuels.
Our innovative Fluidized Bed Concentrator (FBC) technology, combined with Bead Activated Carbon (BAC), effectively captures and recovers this valuable turpentine. Preliminary studies show that the recovered turpentine can be converted into Sustainable Aviation Fuel blends, offering excellent fuel operability and performance characteristics.
Once commercialized, the FBC technology will offer several significant benefits:
- Clean the air: Reduce air pollution at manufacturing sites.
- Reduce fossil fuel energy usage: Enhance energy efficiency in the industry.
- Recover turpentine: Capture and repurpose valuable turpentine.
- Convert turpentine to valuable products: Transform turpentine into biofuels and other useful products.
- Support communities: Provide economic and environmental benefits to rural and underserved communities and opportunity zones.
- Address the climate crisis: Contribute to global efforts in combating climate change.
The resources provided by the Innovation Crossroads program will be instrumental in advancing the development of the FBC technology and turpentine products. With this support, we have the potential to revolutionize an industry currently dominated by outdated, inefficient air pollution control systems. Similar to the transition from old combustion engine cars to modern, efficient hybrids, our FBC systems will replace the antiquated technology with advanced, energy-efficient air pollution control solutions.
Bio:
Kim Tutin is the visionary Founder and CEO of Captis Aire, a company dedicated to commercializing the Fluidized Bed Concentrator (FBC), an advanced air pollution control technology tailored for the wood products industry. Under Kim's passionate and strong leadership, her team has achieved significant milestones, including:
- Successfully completing two pilot runs of the FBC at a commercial wood products manufacturing site.
- Securing a $5 million letter of intent from an FBC customer.
- Acquiring a technology license for the FBC.
As the inventor of the FBC, Kim played a crucial role in filing and defending two patent applications for the technology. Before founding Captis Aire, she held various positions at Georgia-Pacific Chemicals, including chemist, group leader, and technology scout, where she was instrumental in developing new technologies.
Kim holds a bachelor’s degree in Chemistry from the University of Minnesota and an MBA in Technology and Engineering Management from the City University of Seattle.
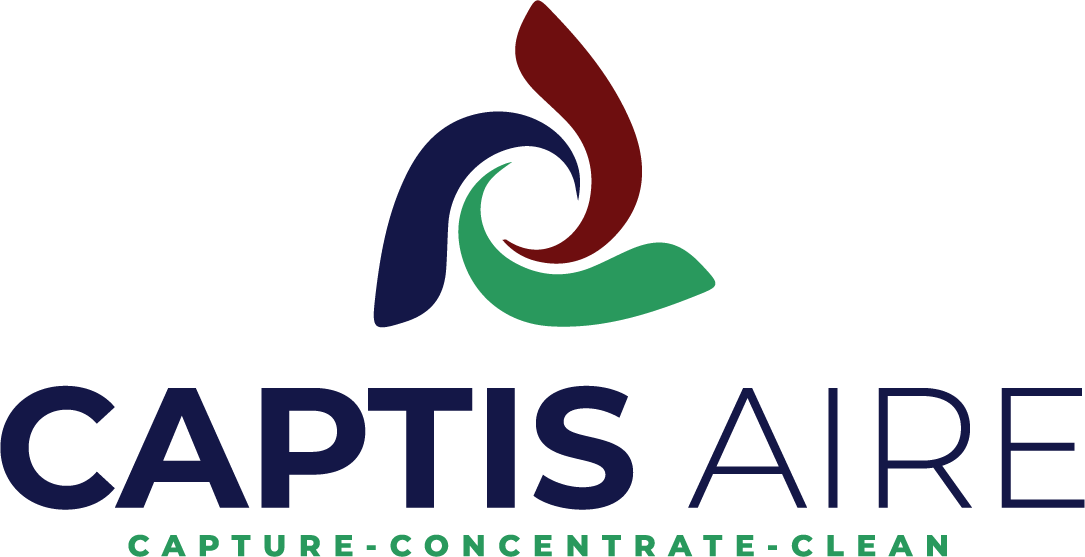
Project Abstract:
As global efforts intensify to reduce air pollutants, Captis Aire is at the forefront with a cutting-edge technology designed to capture air pollutants from wood products manufacturing sites. These sites include producers of liquid biofuels, wood pellets, oriented strand board, plywood, and lumber. A key pollutant released during the wood drying process is turpentine, which is valuable and can be repurposed for various uses, including as biofuels.
Our innovative Fluidized Bed Concentrator (FBC) technology, combined with Bead Activated Carbon (BAC), effectively captures and recovers this valuable turpentine. Preliminary studies show that the recovered turpentine can be converted into Sustainable Aviation Fuel blends, offering excellent fuel operability and performance characteristics.
Once commercialized, the FBC technology will offer several significant benefits:
- Clean the air: Reduce air pollution at manufacturing sites.
- Reduce fossil fuel energy usage: Enhance energy efficiency in the industry.
- Recover turpentine: Capture and repurpose valuable turpentine.
- Convert turpentine to valuable products: Transform turpentine into biofuels and other useful products.
- Support communities: Provide economic and environmental benefits to rural and underserved communities and opportunity zones.
- Address the climate crisis: Contribute to global efforts in combating climate change.
The resources provided by the Innovation Crossroads program will be instrumental in advancing the development of the FBC technology and turpentine products. With this support, we have the potential to revolutionize an industry currently dominated by outdated, inefficient air pollution control systems. Similar to the transition from old combustion engine cars to modern, efficient hybrids, our FBC systems will replace the antiquated technology with advanced, energy-efficient air pollution control solutions.