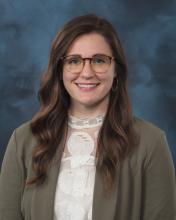
Katy Bradford
Cassette Construction
Katy Bradford is currently an IBUILD Fellow with the DOE Building Technologies Office, researching sustainable construction materials for 3D-printed housing as a doctoral student at the Georgia…
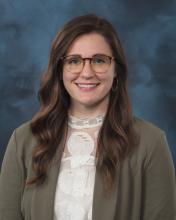
Katy Bradford
Cassette Construction
Katy Bradford is currently an IBUILD Fellow with the DOE Building Technologies Office, researching sustainable construction materials for 3D-printed housing as a doctoral student at the Georgia institute of Technology. She is also a licensed structural engineer with more than five years of experience in the construction industry, including structural design, climate-specific architecture, envelope performance, building component manufacturability, construction product development, and building information modeling. She is passionate about simultaneously reducing the carbon footprint of building materials and improving the availability of affordable housing in the United States.
Project Abstract
Cassette Construction will manufacture low-cost, low-carbon wall and floor panels for modular construction using a custom offsite additive manufacturing process and material. Currently, building construction contributes 9% of global carbon emissions, mainly due to the production of building materials. This equates to 3 billion tons of CO2 released into the atmosphere every year—roughly equivalent to all the passenger cars in the world. Cassette Construction panels utilize bio-based material feedstocks sourced from rapidly growing plants and waste materials, making our products carbon-negative while remaining cost-effective.
Beyond sustainability challenges, the construction industry is facing a massive labor shortage, which contributes in part to the affordable housing crisis in the U.S. By 2031, it is expected that 41% of the workforce will retire. The Cassette Construction
methodology combats this issue by decreasing on-site labor required by up to 89%. This is accomplished by consolidating tasks in the field and removing up to 70% of connections compared to the industry standard wall assembly. Additionally, offsite construction methods enable the rapid fabrication of panels with additive manufacturing methods that will invigorate the construction workforce of the future. In an $11.5 trillion market, it is estimated that these types of gains in efficiency and productivity in an otherwise fragmented industry can result in up to $265 billion in profit each year.
Critical Need for This Technology
- Low-cost, low-carbon structural materials are urgently needed to mitigate the environmental impacts of building construction without sacrificing budgets.
- Accelerating the housing construction timeline with efficient prefabricated building components is essential to meet the growing demand for affordable housing.
- Implementing advanced manufacturing processes in prefabrication can streamline production, minimize waste, and lower costs, ultimately providing quicker and more sustainable housing solutions.
Competition
- Current prefabrication techniques rely on time-consuming framing methods, creating challenges in production scale and quality.
- Existing prefabricated solutions struggle with dimensional accuracy, increasing the chances of rework and delays on the construction site.
- Other prefabricated panels, such as structural insulated panels (SIPs) precast concrete, utilize high-carbon footprint structural and insulation materials.
Key Innovation
An advanced manufacturing process for the offsite fabrication of extruded wall and floor panels made from low-cost, low-carbon building materials.
R&D Status of Product
- Bench-scale proof-of-concept achieved
- Product-market fit validated by customer discovery
Team Overview
- Katy Bradford – Co-Founder and Chief Executive Officer
- Jonathan Valz – Co-Founder Chief Operations Officer
ORNL PI
- Soydan Ozcan – Group Leader, Sustainable Manufacturing Technologies, Energy Science and Technology Directorate
Katy Bradford is currently an IBUILD Fellow with the DOE Building Technologies Office, researching sustainable construction materials for 3D-printed housing as a doctoral student at the Georgia institute of Technology. She is also a licensed structural engineer with more than five years of experience in the construction industry, including structural design, climate-specific architecture, envelope performance, building component manufacturability, construction product development, and building information modeling. She is passionate about simultaneously reducing the carbon footprint of building materials and improving the availability of affordable housing in the United States.
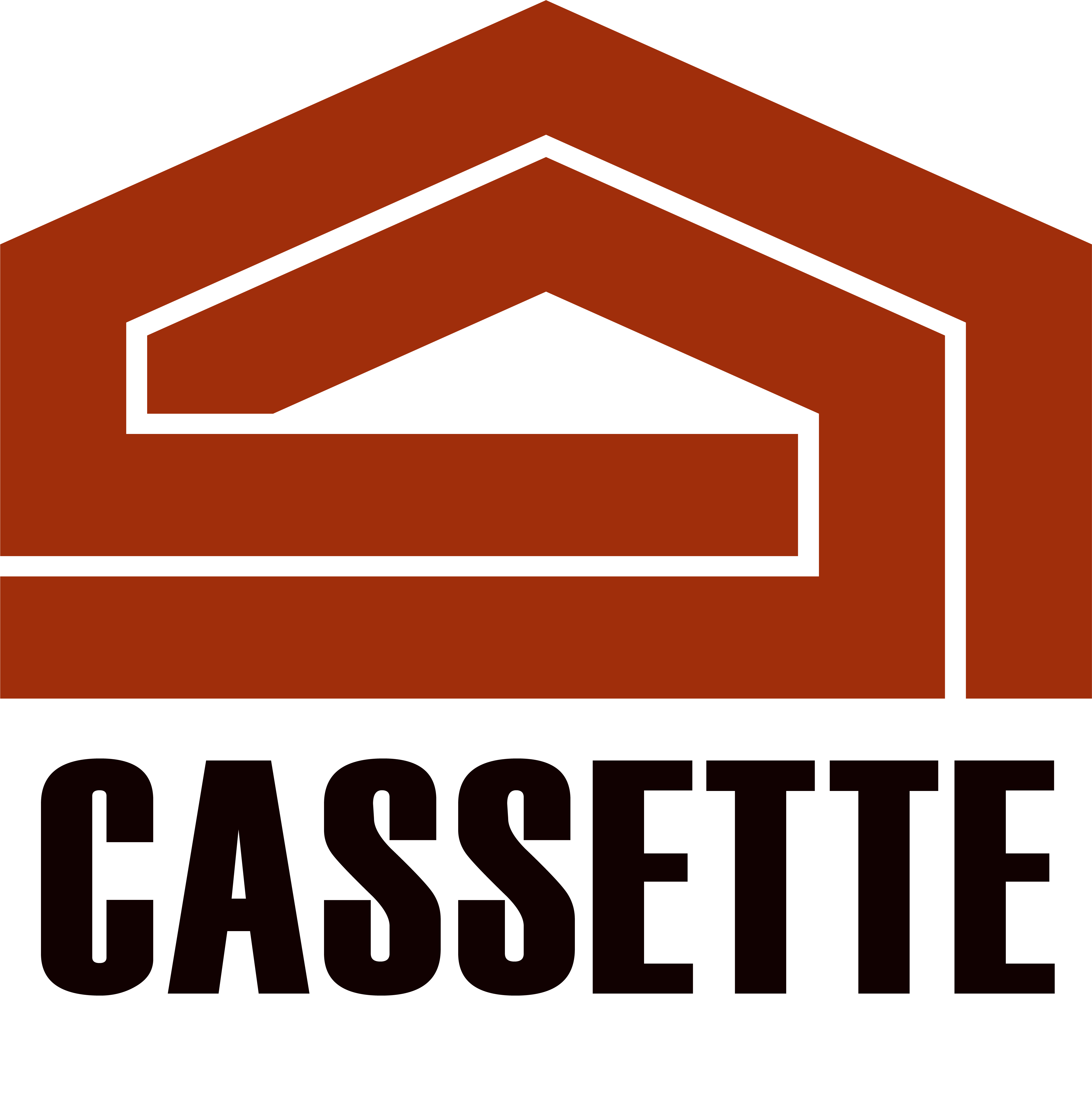
Project Abstract
Cassette Construction will manufacture low-cost, low-carbon wall and floor panels for modular construction using a custom offsite additive manufacturing process and material. Currently, building construction contributes 9% of global carbon emissions, mainly due to the production of building materials. This equates to 3 billion tons of CO2 released into the atmosphere every year—roughly equivalent to all the passenger cars in the world. Cassette Construction panels utilize bio-based material feedstocks sourced from rapidly growing plants and waste materials, making our products carbon-negative while remaining cost-effective.
Beyond sustainability challenges, the construction industry is facing a massive labor shortage, which contributes in part to the affordable housing crisis in the U.S. By 2031, it is expected that 41% of the workforce will retire. The Cassette Construction
methodology combats this issue by decreasing on-site labor required by up to 89%. This is accomplished by consolidating tasks in the field and removing up to 70% of connections compared to the industry standard wall assembly. Additionally, offsite construction methods enable the rapid fabrication of panels with additive manufacturing methods that will invigorate the construction workforce of the future. In an $11.5 trillion market, it is estimated that these types of gains in efficiency and productivity in an otherwise fragmented industry can result in up to $265 billion in profit each year.
Critical Need for This Technology
- Low-cost, low-carbon structural materials are urgently needed to mitigate the environmental impacts of building construction without sacrificing budgets.
- Accelerating the housing construction timeline with efficient prefabricated building components is essential to meet the growing demand for affordable housing.
- Implementing advanced manufacturing processes in prefabrication can streamline production, minimize waste, and lower costs, ultimately providing quicker and more sustainable housing solutions.
Competition
- Current prefabrication techniques rely on time-consuming framing methods, creating challenges in production scale and quality.
- Existing prefabricated solutions struggle with dimensional accuracy, increasing the chances of rework and delays on the construction site.
- Other prefabricated panels, such as structural insulated panels (SIPs) precast concrete, utilize high-carbon footprint structural and insulation materials.
Key Innovation
An advanced manufacturing process for the offsite fabrication of extruded wall and floor panels made from low-cost, low-carbon building materials.
R&D Status of Product
- Bench-scale proof-of-concept achieved
- Product-market fit validated by customer discovery
Team Overview
- Katy Bradford – Co-Founder and Chief Executive Officer
- Jonathan Valz – Co-Founder Chief Operations Officer
ORNL PI
- Soydan Ozcan – Group Leader, Sustainable Manufacturing Technologies, Energy Science and Technology Directorate

Jordan Cannon
Circular Biosciences
Jordan Cannon received his bachelor’s degree in molecular and cellular biology from the University of Illinois at Urbana-Champaign in 2017. Jordan attended the University of Tennessee, Knoxville, to…

Jordan Cannon
Circular Biosciences
Jordan Cannon received his bachelor’s degree in molecular and cellular biology from the University of Illinois at Urbana-Champaign in 2017. Jordan attended the University of Tennessee, Knoxville, to obtain a doctorate in microbiology and is now preparing to defend his dissertation. In his dissertation work, Jordan has focused on the identification, characterization, and protein engineering of bacterial enzymes that can depolymerize PLLA. His research efforts have yielded a diverse catalog of engineered enzymes with potent ability to depolymerize PLLAbased plastics. Jordan plans to apply the enzyme technology he has developed in his doctoral work to reduce plastic waste and help create a sustainable, circular economy for PLLA use.
Project Abstract
Poly-L-lactic acid (PLLA) is currently the most abundant and widely used bioplastic, with production projected to increase approximately five-fold over the next five years. Due to its limited environmental biodegradability, viable disposal options are needed to prevent PLLA from becoming an environmental pollutant. Unlike petroleum-based plastics, PLLA is not being collected in postconsumer waste for recycling, and as a result, it is destined for landfills and composting facilities. However, bioplastics, including PLLA, are currently banned from composting facilities, such as in the city of Knoxville, making landfilling the only end-of-life option for these plastics. This inaccessibility to composting facilities diminishes PLLA's value as a biodegradable commodity and eliminates the key benefit it has over non-biodegradable plastics.
Enzymatic depolymerization is a novel, green approach that provides a sustainable solution to assist in the environmental biodegradation of PLLA. Circular Biosciences has developed a catalog of engineered protease enzymes capable of depolymerizing PLLA at ambient temperatures under mild reaction conditions. The company’s current objective is to further engineer a catalog of highly potent PLLA depolymerizing enzymes that can survive elevated temperatures for use in high-temperature applications. Specifically, the company aims to engineer and/or immobilize enzymes that can be integrated into PLLA during the extrusion process. By doing so, the enzymes can be turned into an additive that enhances the biodegradation of PLLA waste destined for landfills, home composting, or the natural environment if mismanaged by consumers.
Leveraging the technical expertise and knowledge at ORNL would allow Circular Biosciences to translate its enzyme technology into a viable product, promoting sustainable management and disposal of PLLA bioplastics.
Critical Need for This Technology
- Improvements in thermostability of enzymes for applications in polylactic acid extrusion
- Novel enzyme immobilization techniques for the polylactic acid extrusion process
- Scaling production of polylactic acid materials containing immobilized enzymes
Key Innovation
- Development of enzymes capable of rapidly degrading polylactic acid (PLA) films overnight at ambient temperatures, resulting in soluble and environmentally benign end products.
- Identification of several enzymes in our catalog that outperform Proteinase K, the academic and industry standard for enzymatic PLA degradation.
- Implementation of a cost-effective methodology for quantifying the PLA degradation product, L-lactic acid.
R&D Status of Product
- Our current enzyme catalog contains over 100 engineered variants of three naturally occurring enzymes.
- Several enzyme variants demonstrate more than five times greater activity than Proteinase K at ambient temperature.
- One enzyme variant has been engineered with enhanced thermostability, exhibiting a temperature increase of 15-20°C relative to the original enzyme.
Team Overview
- Jordan Cannon – Founder and Chief Executive Officer
ORNL PI
- Yue Yuan – Distinguished Staff Fellowship Program, Macromolecular Nanomaterials, Physical Sciences Directorate
Jordan Cannon received his bachelor’s degree in molecular and cellular biology from the University of Illinois at Urbana-Champaign in 2017. Jordan attended the University of Tennessee, Knoxville, to obtain a doctorate in microbiology and is now preparing to defend his dissertation. In his dissertation work, Jordan has focused on the identification, characterization, and protein engineering of bacterial enzymes that can depolymerize PLLA. His research efforts have yielded a diverse catalog of engineered enzymes with potent ability to depolymerize PLLAbased plastics. Jordan plans to apply the enzyme technology he has developed in his doctoral work to reduce plastic waste and help create a sustainable, circular economy for PLLA use.
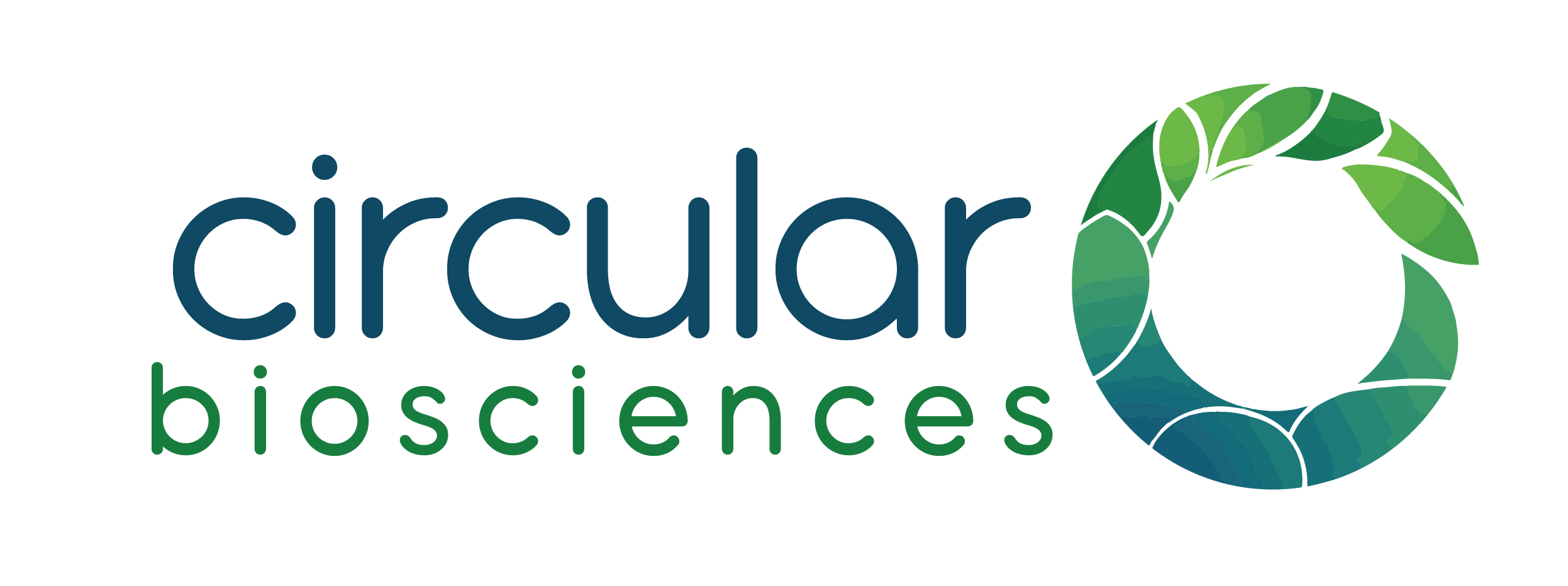
Project Abstract
Poly-L-lactic acid (PLLA) is currently the most abundant and widely used bioplastic, with production projected to increase approximately five-fold over the next five years. Due to its limited environmental biodegradability, viable disposal options are needed to prevent PLLA from becoming an environmental pollutant. Unlike petroleum-based plastics, PLLA is not being collected in postconsumer waste for recycling, and as a result, it is destined for landfills and composting facilities. However, bioplastics, including PLLA, are currently banned from composting facilities, such as in the city of Knoxville, making landfilling the only end-of-life option for these plastics. This inaccessibility to composting facilities diminishes PLLA's value as a biodegradable commodity and eliminates the key benefit it has over non-biodegradable plastics.
Enzymatic depolymerization is a novel, green approach that provides a sustainable solution to assist in the environmental biodegradation of PLLA. Circular Biosciences has developed a catalog of engineered protease enzymes capable of depolymerizing PLLA at ambient temperatures under mild reaction conditions. The company’s current objective is to further engineer a catalog of highly potent PLLA depolymerizing enzymes that can survive elevated temperatures for use in high-temperature applications. Specifically, the company aims to engineer and/or immobilize enzymes that can be integrated into PLLA during the extrusion process. By doing so, the enzymes can be turned into an additive that enhances the biodegradation of PLLA waste destined for landfills, home composting, or the natural environment if mismanaged by consumers.
Leveraging the technical expertise and knowledge at ORNL would allow Circular Biosciences to translate its enzyme technology into a viable product, promoting sustainable management and disposal of PLLA bioplastics.
Critical Need for This Technology
- Improvements in thermostability of enzymes for applications in polylactic acid extrusion
- Novel enzyme immobilization techniques for the polylactic acid extrusion process
- Scaling production of polylactic acid materials containing immobilized enzymes
Key Innovation
- Development of enzymes capable of rapidly degrading polylactic acid (PLA) films overnight at ambient temperatures, resulting in soluble and environmentally benign end products.
- Identification of several enzymes in our catalog that outperform Proteinase K, the academic and industry standard for enzymatic PLA degradation.
- Implementation of a cost-effective methodology for quantifying the PLA degradation product, L-lactic acid.
R&D Status of Product
- Our current enzyme catalog contains over 100 engineered variants of three naturally occurring enzymes.
- Several enzyme variants demonstrate more than five times greater activity than Proteinase K at ambient temperature.
- One enzyme variant has been engineered with enhanced thermostability, exhibiting a temperature increase of 15-20°C relative to the original enzyme.
Team Overview
- Jordan Cannon – Founder and Chief Executive Officer
ORNL PI
- Yue Yuan – Distinguished Staff Fellowship Program, Macromolecular Nanomaterials, Physical Sciences Directorate
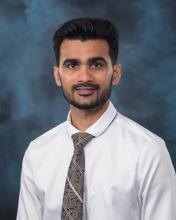
Vinit Chaudhary
Elemental Composites LLC
Vinit Chaudhary, a mechanical engineer turned entrepreneur, is passionate about pioneering sustainable advanced materials in the composites industry. In 2025, he founded Elemental Composites LLC…
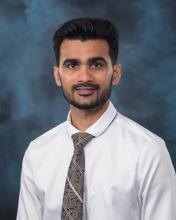
Vinit Chaudhary
Elemental Composites LLC
Vinit Chaudhary, a mechanical engineer turned entrepreneur, is passionate about pioneering sustainable advanced materials in the composites industry. In 2025, he founded Elemental Composites LLC , building on research conducted during his master’s program. Vinit earned both his bachelor’s and master’s degrees in mechanical engineering from the University of Tennessee, Knoxville. He brings five years of experience in designing and manufacturing advanced composites to his role, where he focuses on product development and expanding technology applications. Drawing from a family legacy in retail entrepreneurship, Vinit excels in perseverance, networking, and business strategy.
Project Abstract
Elemental Composites LLC excels in producing nonwoven mats tailored for fiber-reinforced composites. By precisely aligning and blending fibers, Elemental Composites creates anisotropic nonwoven mats with uniform fiber distribution, offering superior performance and consistency. Their innovative manufacturing process accommodates a wide range of reinforcing fibers—including carbon, glass, and natural fibers like bamboo, hemp, wool, banana, and flax—as well as various thermoplastic polymers such as polypropylene, polyamide, and polyphenylene sulfide.
Elemental Composites' technology stands out for its versatility and commitment to sustainable practices. It enables the production of lightweight, high-performance aligned nonwoven preforms suitable for diverse applications, including automotive, marine, infrastructure, wind energy, transportation, sporting goods, and medical equipment.
A key advantage of Elemental Composites' approach is its ability to use fibers up to 250 mm (10 inches) long, significantly surpassing the typical 25 mm limit of conventional nonwoven manufacturing methods. Additionally, Elemental Composites' products can achieve densities of up to 1,500 grams per square meter (gsm), compared to the 300 gsm limit of traditional nonwovens. This allows for the creation of high-performance materials with greater efficiency and less material.
We Are Looking For
- Early adopters to trial and provide feedback on our natural fiber intermediate products
- Collaborative partners to assist in transforming our intermediate products into final prototype composite components
- Expertise in branding and marketing to help position and promote our products effectively
- Government funding to support further development and commercialization efforts
Critical Need for This Technology
The composite materials market is growing rapidly, with projections estimating it will reach $160 billion by 2027. Unfortunately, a large portion of these composites ends up in landfills at the end of their lifecycle, which is both environmentally harmful and a waste of valuable materials and the energy used in their production.
We are committed to a sustainable future by focusing on recycling high-quality materials and advancing natural fiber composites. These composites offer significant benefits, including eco-friendliness, lightweight characteristics, cost-efficiency, and biodegradability, making them a viable solution for the industry's sustainability challenges.
Our technology addresses these issues by using short, chopped fibers, which provide a more cost-effective and energy-efficient alternative to traditional, expensive continuous fibers, enhancing overall performance and reducing environmental impact.
Competition
Conventional nonwoven technologies, such as paper making, air-laid, extrusion-compression, and SMC, produce isotropic nonwovens with uniform mechanical properties in all directions. In contrast, our technology achieves superior mechanical performance through precise control of fiber orientation, allowing for three-dimensional anisotropy. This results in enhanced properties in both the in-plane and transverse directions.
While existing nonwoven methods are constrained to fibers of 1–2 inches and produce fabrics with a maximum density of 300 grams per square meter (gsm), our process accommodates fibers up to 10 inches in length and can produce nonwovens up to 1500 gsm. This capability not only enhances performance but also improves cost-effectiveness by allowing for greater material density in smaller areas.
Additionally, although injection molding can improve fiber orientation, it often results in significant fiber length reduction due to attrition. Our process preserves fiber length more effectively, leading to better mechanical properties and maintaining high performance throughout.
Key Innovation
Our key innovation lies in a proprietary non-contact mixing process that enables the incorporation of multiple fiber types into a homogeneous feedstock. This uniform feedstock is essential for producing consistent intermediate products.
The non-contact nature of our mixing process is particularly advantageous as it preserves fiber length, even in brittle fibers like carbon and glass fibers. Additionally, it effectively deagglomerates fiber bundles into individual fibers, enhancing processability and ensuring high-quality outcomes in our manufacturing process.
R&D Status of Product
We have successfully demonstrated proof-of-concept for several fiber systems with our lab-scale equipment. Additionally, we have access to industrial-scale machinery for producing nonwovens and yarns using coir (coconut) fibers. Currently, we are focused on integrating a broader range of fiber types into our production-scale equipment and are developing proof-of-concept composite prototype parts to validate and refine our technology.
Team Overview
- Vinit Chaudhary – Founder and CEO
ORNL PI
- Soydan Ozcan – Group Leader, Sustainable Manufacturing Technologies, Energy Science and Technology Directorate
- Uday Vaidya – Governor's Chair, Composite Manufacturing, Energy Science and Technology Directorate
Vinit Chaudhary, a mechanical engineer turned entrepreneur, is passionate about pioneering sustainable advanced materials in the composites industry. In 2025, he founded Elemental Composites LLC , building on research conducted during his master’s program. Vinit earned both his bachelor’s and master’s degrees in mechanical engineering from the University of Tennessee, Knoxville. He brings five years of experience in designing and manufacturing advanced composites to his role, where he focuses on product development and expanding technology applications. Drawing from a family legacy in retail entrepreneurship, Vinit excels in perseverance, networking, and business strategy.
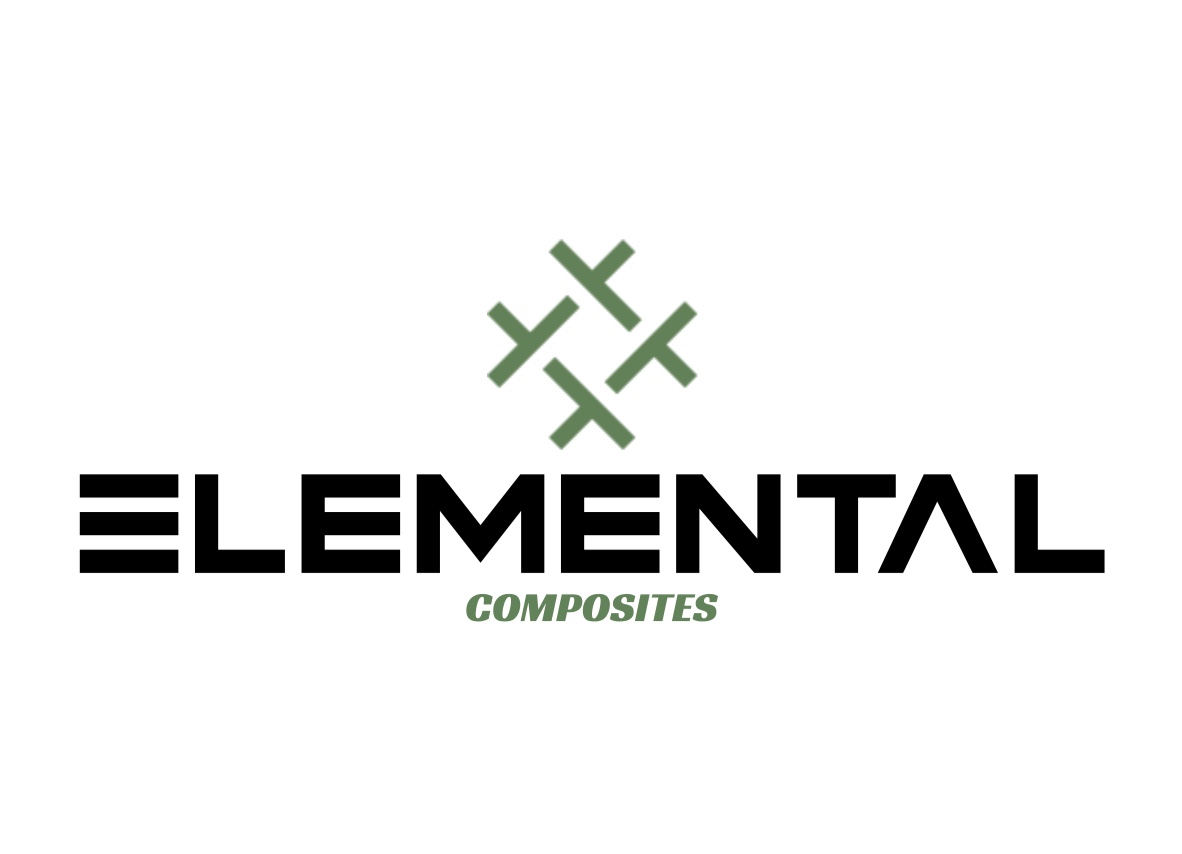
Project Abstract
Elemental Composites LLC excels in producing nonwoven mats tailored for fiber-reinforced composites. By precisely aligning and blending fibers, Elemental Composites creates anisotropic nonwoven mats with uniform fiber distribution, offering superior performance and consistency. Their innovative manufacturing process accommodates a wide range of reinforcing fibers—including carbon, glass, and natural fibers like bamboo, hemp, wool, banana, and flax—as well as various thermoplastic polymers such as polypropylene, polyamide, and polyphenylene sulfide.
Elemental Composites' technology stands out for its versatility and commitment to sustainable practices. It enables the production of lightweight, high-performance aligned nonwoven preforms suitable for diverse applications, including automotive, marine, infrastructure, wind energy, transportation, sporting goods, and medical equipment.
A key advantage of Elemental Composites' approach is its ability to use fibers up to 250 mm (10 inches) long, significantly surpassing the typical 25 mm limit of conventional nonwoven manufacturing methods. Additionally, Elemental Composites' products can achieve densities of up to 1,500 grams per square meter (gsm), compared to the 300 gsm limit of traditional nonwovens. This allows for the creation of high-performance materials with greater efficiency and less material.
We Are Looking For
- Early adopters to trial and provide feedback on our natural fiber intermediate products
- Collaborative partners to assist in transforming our intermediate products into final prototype composite components
- Expertise in branding and marketing to help position and promote our products effectively
- Government funding to support further development and commercialization efforts
Critical Need for This Technology
The composite materials market is growing rapidly, with projections estimating it will reach $160 billion by 2027. Unfortunately, a large portion of these composites ends up in landfills at the end of their lifecycle, which is both environmentally harmful and a waste of valuable materials and the energy used in their production.
We are committed to a sustainable future by focusing on recycling high-quality materials and advancing natural fiber composites. These composites offer significant benefits, including eco-friendliness, lightweight characteristics, cost-efficiency, and biodegradability, making them a viable solution for the industry's sustainability challenges.
Our technology addresses these issues by using short, chopped fibers, which provide a more cost-effective and energy-efficient alternative to traditional, expensive continuous fibers, enhancing overall performance and reducing environmental impact.
Competition
Conventional nonwoven technologies, such as paper making, air-laid, extrusion-compression, and SMC, produce isotropic nonwovens with uniform mechanical properties in all directions. In contrast, our technology achieves superior mechanical performance through precise control of fiber orientation, allowing for three-dimensional anisotropy. This results in enhanced properties in both the in-plane and transverse directions.
While existing nonwoven methods are constrained to fibers of 1–2 inches and produce fabrics with a maximum density of 300 grams per square meter (gsm), our process accommodates fibers up to 10 inches in length and can produce nonwovens up to 1500 gsm. This capability not only enhances performance but also improves cost-effectiveness by allowing for greater material density in smaller areas.
Additionally, although injection molding can improve fiber orientation, it often results in significant fiber length reduction due to attrition. Our process preserves fiber length more effectively, leading to better mechanical properties and maintaining high performance throughout.
Key Innovation
Our key innovation lies in a proprietary non-contact mixing process that enables the incorporation of multiple fiber types into a homogeneous feedstock. This uniform feedstock is essential for producing consistent intermediate products.
The non-contact nature of our mixing process is particularly advantageous as it preserves fiber length, even in brittle fibers like carbon and glass fibers. Additionally, it effectively deagglomerates fiber bundles into individual fibers, enhancing processability and ensuring high-quality outcomes in our manufacturing process.
R&D Status of Product
We have successfully demonstrated proof-of-concept for several fiber systems with our lab-scale equipment. Additionally, we have access to industrial-scale machinery for producing nonwovens and yarns using coir (coconut) fibers. Currently, we are focused on integrating a broader range of fiber types into our production-scale equipment and are developing proof-of-concept composite prototype parts to validate and refine our technology.
Team Overview
- Vinit Chaudhary – Founder and CEO
ORNL PI
- Soydan Ozcan – Group Leader, Sustainable Manufacturing Technologies, Energy Science and Technology Directorate
- Uday Vaidya – Governor's Chair, Composite Manufacturing, Energy Science and Technology Directorate
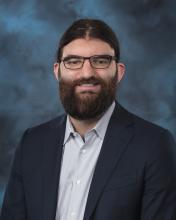
Brian Iezzi
Fibarcode
Brian Iezzi leads the development of Fibarcode, a unique and indelible textile labeling method designed for authentication, traceability, and end-of-use management. With over ten years of experience…
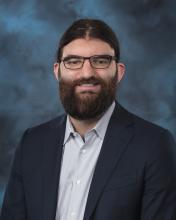
Brian Iezzi
Fibarcode
Brian Iezzi leads the development of Fibarcode, a unique and indelible textile labeling method designed for authentication, traceability, and end-of-use management. With over ten years of experience in textile manufacturing and materials research and development, Brian has a rich background that includes developing novel yarns as an intern at the Gaston College Textile Technology Center and currently serving as an R&D engineer at Parkdale Mills, the largest yarn manufacturer in the western hemisphere.
Brian earned his bachelor's degree in textile engineering from North Carolina State University and a doctorate in materials science and engineering from the University of Michigan. During an internship with the Defense Fabric Discovery Center at MIT’s Lincoln Laboratory, he co-invented the Fibarcode technology. His efforts have secured $175,000 in state and federal grants to support Fibarcode's development, including funding from the Michigan Translational Research and Commercialization program, UM Graham Sustainability Institute Catalyst grant, NextCycle Michigan Accelerator, and the National Science Foundation I-Corps program.
In his spare time, Brian has co-organized life cycle assessment educational workshops in Kenya, Tanzania, and Senegal for the African Materials Research Society. He also enjoys cooking, climbing, and mountain biking.
Project Abstract
This project aims to tackle the rapidly growing issue of textile waste in the United States, which has seen an 80% increase in landfill contributions since 2000. Despite significant investments in circular methods of reuse, repair, and recycling, the implementation of these systems is hindered by insufficient information transfer from manufacturing to the end of an item's lifecycle. A major contributor to this issue is the lack of robust and detailed labeling, with recent studies revealing that nearly 30% of end-of-life textiles lack legible care and content labels, and over 40% of existing labels inaccurately describe the material content.
To address these challenges, our project focuses on developing more accurate and durable labeling for apparel items, ensuring continuous data transfer from manufacturing to post-consumer stages. Our innovative solution is an engineered photonic "barcode" integrated into a fiber, which can be seamlessly incorporated into fabrics and apparel using standard textile manufacturing processes like weaving, knitting, or stitching. This photonic fiber barcode, or Fibarcode, can be scanned with handheld, portable spectroscopic systems, providing an indelible method of communicating critical item-level information from production to post-consumer collection, sorting, and recycling.
The Fibarcode technology has the potential to automate the identification and sorting of post-consumer textiles into appropriate categories, a crucial step in capturing the estimated $100 billion annual value of landfilled apparel. Additionally, initial market research suggests this technology could have further applications in anti-counterfeiting, medical garments, military uniforms for signature management, and supply chain traceability.
We Are Looking For
- Partnerships with brands interested in piloting our technology with their product with a hopeful intended use case of full life cycle product traceability, end of use identification and sorting, and/or anti-counterfeiting
- Developing a customer-validated business model and financial projections
- Potential additional application areas where this platform technology could be useful
Critical Need for This Technology
- Material Waste: Currently, only 1% of the material used to produce clothing is recycled into new clothing, resulting in more than $100 billion worth of materials wasted annually (Ellen MacArthur Foundation).
- Labeling Issues: A study examining over 10,000 post-consumer apparel items found that nearly 30% lacked a readable label. Furthermore, among the items with labels, over 40% inaccurately described the material content (Fashion for Good).
- Industry Challenge: "We are really trying to figure out the 'process' for how end-of-life is going to happen. Identification of components is going to be a major hurdle – from the beginning, we have believed that we need to find a way to put a serial number on every component! I have done more digging into what you are working on – and really believe you are on the right path." – Recycling Partner
Competition
- QR Codes face a similar challenge as current, standard printed labels. They can be detached or will fade over time and are also susceptible to counterfeiting.
- RFID tags are composed of integrated circuits and printed metal antennas which leads to significant cost which has prevented market adoption at the item level and can also disrupt recycling. Furthermore, embedding RFID into an item permanently (vs using in retail alone) has significant consumer privacy concerns.
Key Innovation
Our solution creates a fiber with a spectroscopic “barcode” integrated in its interior, produced at scale, and readily interlaced directly into fabrics and apparel using standard textile manufacturing processes. The barcode provides a unique identifier via rapid readout. It uses an all-polymer, fully recyclable composition, and is potentially compatible with existing optical sorting equipment, maximizing integration and scalability of the system.
R&D Status of Product
- Current Stage: The product is currently at Technology Readiness Level (TRL) 3, with successful integration of the fiber barcode into relevant textiles.
- Future Goals: The aim is to develop a complete prototype system, including scanning and software, within the next two years, reaching TRL 5 and ready for commercial pilots.
Team Overview
- Brian Iezzi – Founder
- Yash Dadeech – Prototype Development, Graduate Student at University of Michigan
- Max Shtein – Technical Advisor, Professor at University of Michigan
ORNL PI
- Merlin Theodore – Group Leader, Advanced Fibers Manufacturing, Energy Science and Technology Directorate
Brian Iezzi leads the development of Fibarcode, a unique and indelible textile labeling method designed for authentication, traceability, and end-of-use management. With over ten years of experience in textile manufacturing and materials research and development, Brian has a rich background that includes developing novel yarns as an intern at the Gaston College Textile Technology Center and currently serving as an R&D engineer at Parkdale Mills, the largest yarn manufacturer in the western hemisphere.
Brian earned his bachelor's degree in textile engineering from North Carolina State University and a doctorate in materials science and engineering from the University of Michigan. During an internship with the Defense Fabric Discovery Center at MIT’s Lincoln Laboratory, he co-invented the Fibarcode technology. His efforts have secured $175,000 in state and federal grants to support Fibarcode's development, including funding from the Michigan Translational Research and Commercialization program, UM Graham Sustainability Institute Catalyst grant, NextCycle Michigan Accelerator, and the National Science Foundation I-Corps program.
In his spare time, Brian has co-organized life cycle assessment educational workshops in Kenya, Tanzania, and Senegal for the African Materials Research Society. He also enjoys cooking, climbing, and mountain biking.
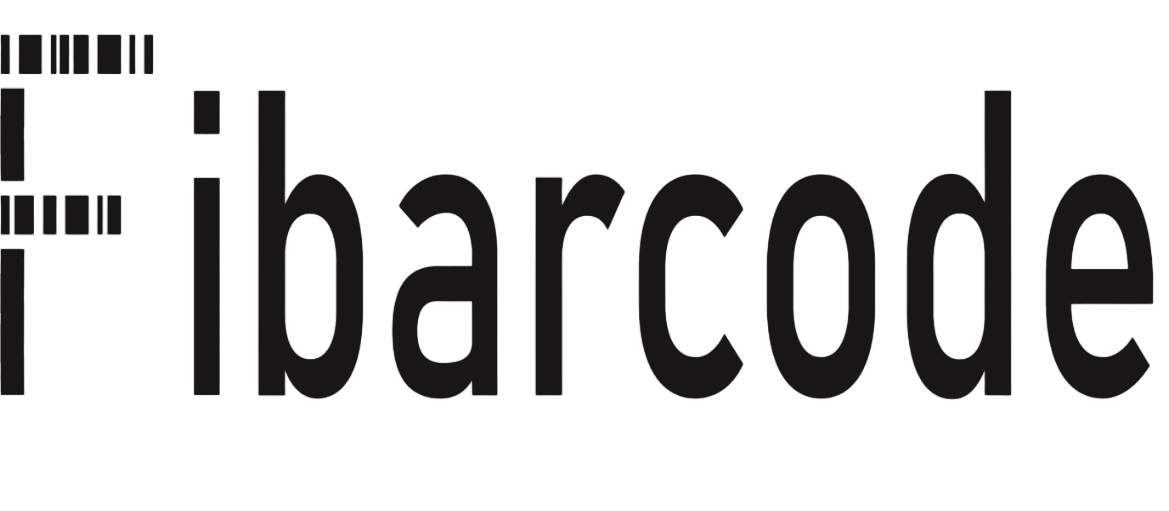
Project Abstract
This project aims to tackle the rapidly growing issue of textile waste in the United States, which has seen an 80% increase in landfill contributions since 2000. Despite significant investments in circular methods of reuse, repair, and recycling, the implementation of these systems is hindered by insufficient information transfer from manufacturing to the end of an item's lifecycle. A major contributor to this issue is the lack of robust and detailed labeling, with recent studies revealing that nearly 30% of end-of-life textiles lack legible care and content labels, and over 40% of existing labels inaccurately describe the material content.
To address these challenges, our project focuses on developing more accurate and durable labeling for apparel items, ensuring continuous data transfer from manufacturing to post-consumer stages. Our innovative solution is an engineered photonic "barcode" integrated into a fiber, which can be seamlessly incorporated into fabrics and apparel using standard textile manufacturing processes like weaving, knitting, or stitching. This photonic fiber barcode, or Fibarcode, can be scanned with handheld, portable spectroscopic systems, providing an indelible method of communicating critical item-level information from production to post-consumer collection, sorting, and recycling.
The Fibarcode technology has the potential to automate the identification and sorting of post-consumer textiles into appropriate categories, a crucial step in capturing the estimated $100 billion annual value of landfilled apparel. Additionally, initial market research suggests this technology could have further applications in anti-counterfeiting, medical garments, military uniforms for signature management, and supply chain traceability.
We Are Looking For
- Partnerships with brands interested in piloting our technology with their product with a hopeful intended use case of full life cycle product traceability, end of use identification and sorting, and/or anti-counterfeiting
- Developing a customer-validated business model and financial projections
- Potential additional application areas where this platform technology could be useful
Critical Need for This Technology
- Material Waste: Currently, only 1% of the material used to produce clothing is recycled into new clothing, resulting in more than $100 billion worth of materials wasted annually (Ellen MacArthur Foundation).
- Labeling Issues: A study examining over 10,000 post-consumer apparel items found that nearly 30% lacked a readable label. Furthermore, among the items with labels, over 40% inaccurately described the material content (Fashion for Good).
- Industry Challenge: "We are really trying to figure out the 'process' for how end-of-life is going to happen. Identification of components is going to be a major hurdle – from the beginning, we have believed that we need to find a way to put a serial number on every component! I have done more digging into what you are working on – and really believe you are on the right path." – Recycling Partner
Competition
- QR Codes face a similar challenge as current, standard printed labels. They can be detached or will fade over time and are also susceptible to counterfeiting.
- RFID tags are composed of integrated circuits and printed metal antennas which leads to significant cost which has prevented market adoption at the item level and can also disrupt recycling. Furthermore, embedding RFID into an item permanently (vs using in retail alone) has significant consumer privacy concerns.
Key Innovation
Our solution creates a fiber with a spectroscopic “barcode” integrated in its interior, produced at scale, and readily interlaced directly into fabrics and apparel using standard textile manufacturing processes. The barcode provides a unique identifier via rapid readout. It uses an all-polymer, fully recyclable composition, and is potentially compatible with existing optical sorting equipment, maximizing integration and scalability of the system.
R&D Status of Product
- Current Stage: The product is currently at Technology Readiness Level (TRL) 3, with successful integration of the fiber barcode into relevant textiles.
- Future Goals: The aim is to develop a complete prototype system, including scanning and software, within the next two years, reaching TRL 5 and ready for commercial pilots.
Team Overview
- Brian Iezzi – Founder
- Yash Dadeech – Prototype Development, Graduate Student at University of Michigan
- Max Shtein – Technical Advisor, Professor at University of Michigan
ORNL PI
- Merlin Theodore – Group Leader, Advanced Fibers Manufacturing, Energy Science and Technology Directorate
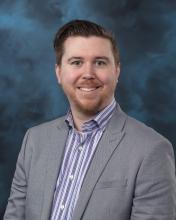
Kevin Roccapriore
AtomQ
Kevin Roccapriore is the president and co-founder of AtomQ, Inc. AtomQ was started through his work as an R&D associate with collaboration from the user program at ORNL in the data nanoanalytics…
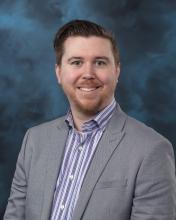
Kevin Roccapriore
AtomQ
Kevin Roccapriore is the president and co-founder of AtomQ, Inc. AtomQ was started through his work as an R&D associate with collaboration from the user program at ORNL in the data nanoanalytics group in the Center for Nanophase Materials Sciences, a DOE user facility. His research has focused on combining the scanning transmission electron microscope (STEM) with both machine intelligence and custom hardware control to automate, understand, and precisely control the interaction of the electron beam with matter at the atomic scale with a focus on tuning optical properties. Prior to his professional career, he received his bachelor’s in food science from the University of Florida in 2011, as well as a master’s (2014) and doctorate (2018) in physics from the University of North Texas. Through his professional experience, he has had both fruitful academic and industry collaborations, enabling successful use of
STEM to identify and target single atoms in real time and manipulate matter literally atom by atom, forming the basis for AtomQ’s technology.
Project Abstract
Quantum computing, a revolutionary paradigm that leverages quantum mechanics, enables calculations at unprecedented speeds, tackling complex and currently unsolvable problems. However, current quantum computing relies on diverse architectures for constructing and connecting qubits—the fundamental units of quantum computation. For example, IonQ uses trapped ion technology, while IBM and Google employ superconducting microwave circuitry. Although quantum computers already exist, the largest systems to date consist of about 1,000 qubits and occupy a large room. To address meaningful world problems in areas such as energy, pharmaceutical research, finance, and cryptography, quantum computers will require at least 1 million qubits, making scalability a critical challenge.
AtomQ aims to solve this scalability issue by developing a scalable atomic quantum computer utilizing large numbers of optically active quantum defects created via scanning transmission electron microscopy. The platform, developed by AtomQ’s co-founders, generates color centers (a type of qubit active in the telecom band) at the single-atom level with millisecond precision and atomic accuracy. This capability allows for the creation of much larger arrays of qubits, enabling their design, construction, and integration within a single compact device. Such advancements could lead to the large-scale fabrication of atomically designed quantum devices, akin to the chip-scale production of silicon transistors.
We Are Looking For
Strategic partnerships
Investment
New team members (silicon photonics design)
Critical Need for This Technology
Addressing complex problems across various fields often involves navigating vast parameter spaces. Examples include:
- Materials Science: Identifying optimal materials for advanced applications such as fusion confinement, battery electrodes, or solar cells.
- Logistics: Enhancing fuel efficiency and optimizing the transportation of goods, including solving challenges like the traveling salesman problem and improving airline travel.
- Security: Ensuring safe communication, implementing unbreakable data encryption, and enabling quantum key distribution.
- Finance: Optimizing financial portfolios and managing risk with precision.
Classical computing is not suitable for some of the world’s most sophisticated problems – this is where quantum computing steps in. With AtomQ technology, we aim to produce atomically defined and identical qubits - at scale - allowing us to achieve a fully scalable atomic quantum computer in order to appropriately address and tackle these diverse and complex problems.
Competition
Competing technologies in the quantum computing landscape include:
- Superconducting Circuitry: Utilizes superconducting materials to create qubits with high coherence times and fast gate speeds.
- Optically Trapped Neutral Atoms: Employs laser fields to trap and manipulate neutral atoms, enabling quantum computation with high fidelity.
- Electrostatically Trapped Ions: Uses electromagnetic fields to confine and control ions, facilitating precise quantum operations and error correction.
- Silicon T-Centres: Leverages defect centers in silicon for quantum information processing, offering potential for integration with existing silicon-based technologies.
These technologies represent the forefront of quantum computing advancements, each with its own strengths and challenges.
Key Innovation
AtomQ’s key innovation is deterministic creation of identical atomic quantum defects in the solid state at scale. No other approach in creation of qubits - the fundamental building block of a quantum computer - is both truly atomic and compatible with silicon technologies. Due to the precision and control of the distribution of electrons in aberration corrected electron microscopes, AtomQ is able to precisely deliver electrons in space and time, allowing to build identical structures atom by atom. For these reasons, we believe AtomQ is the first of its kind to have the potential to build truly scalable quantum computers.
R&D Status of Product
AtomQ is currently in the prototyping phase, undergoing optical evaluation, and integration into semiconducting and photonic circuitry.
Team Overview
- Kevin Roccapriore – Co-founder and President
ORNL PI
- Travis Humble – Director, Quantum Science Center, Computing and Computational Sciences Directorate
- Andrew Lupini – Group Leader, Scanning Transmission Electron Microscope, Physical Sciences Directorate
Kevin Roccapriore is the president and co-founder of AtomQ, Inc. AtomQ was started through his work as an R&D associate with collaboration from the user program at ORNL in the data nanoanalytics group in the Center for Nanophase Materials Sciences, a DOE user facility. His research has focused on combining the scanning transmission electron microscope (STEM) with both machine intelligence and custom hardware control to automate, understand, and precisely control the interaction of the electron beam with matter at the atomic scale with a focus on tuning optical properties. Prior to his professional career, he received his bachelor’s in food science from the University of Florida in 2011, as well as a master’s (2014) and doctorate (2018) in physics from the University of North Texas. Through his professional experience, he has had both fruitful academic and industry collaborations, enabling successful use of
STEM to identify and target single atoms in real time and manipulate matter literally atom by atom, forming the basis for AtomQ’s technology.
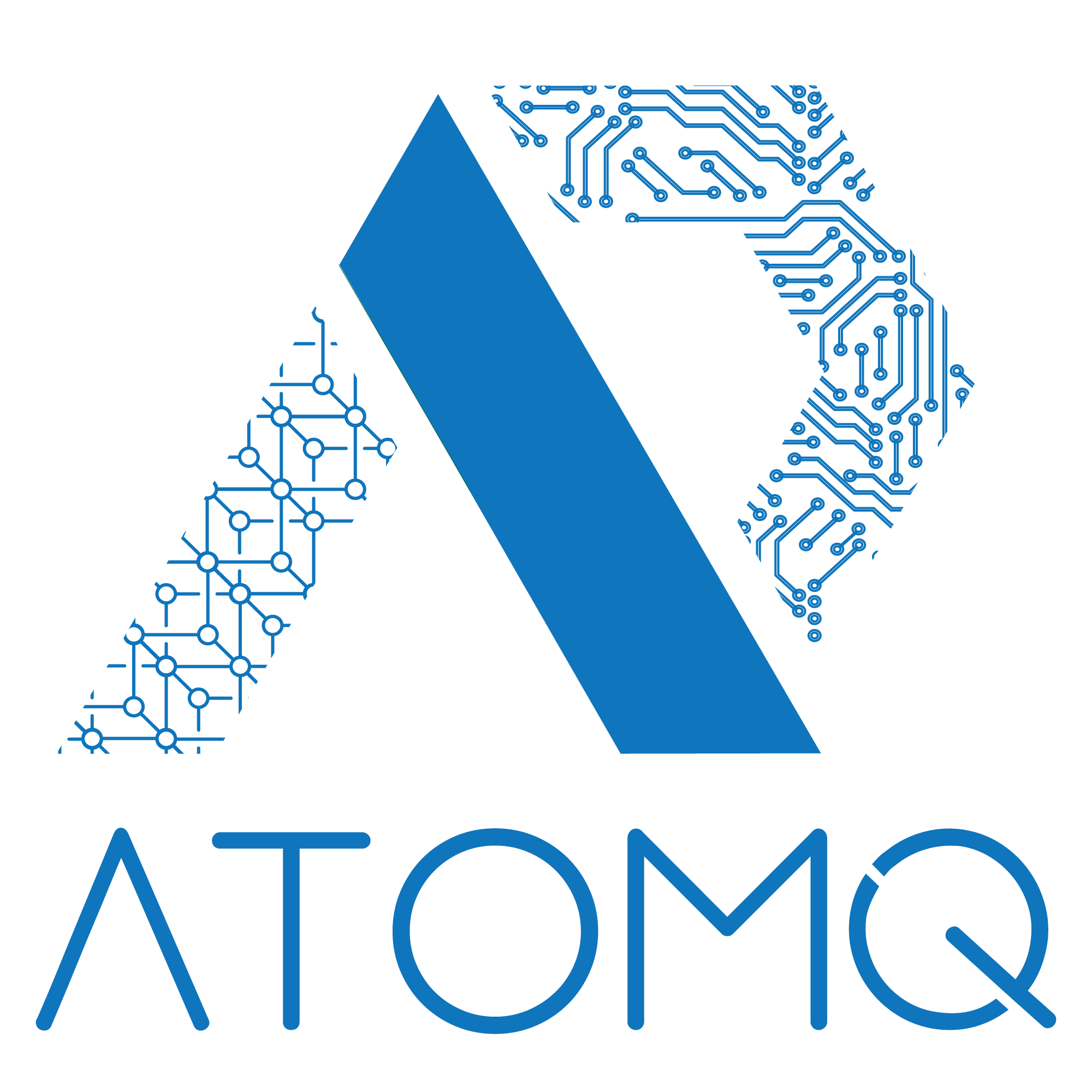
Project Abstract
Quantum computing, a revolutionary paradigm that leverages quantum mechanics, enables calculations at unprecedented speeds, tackling complex and currently unsolvable problems. However, current quantum computing relies on diverse architectures for constructing and connecting qubits—the fundamental units of quantum computation. For example, IonQ uses trapped ion technology, while IBM and Google employ superconducting microwave circuitry. Although quantum computers already exist, the largest systems to date consist of about 1,000 qubits and occupy a large room. To address meaningful world problems in areas such as energy, pharmaceutical research, finance, and cryptography, quantum computers will require at least 1 million qubits, making scalability a critical challenge.
AtomQ aims to solve this scalability issue by developing a scalable atomic quantum computer utilizing large numbers of optically active quantum defects created via scanning transmission electron microscopy. The platform, developed by AtomQ’s co-founders, generates color centers (a type of qubit active in the telecom band) at the single-atom level with millisecond precision and atomic accuracy. This capability allows for the creation of much larger arrays of qubits, enabling their design, construction, and integration within a single compact device. Such advancements could lead to the large-scale fabrication of atomically designed quantum devices, akin to the chip-scale production of silicon transistors.
We Are Looking For
Strategic partnerships
Investment
New team members (silicon photonics design)
Critical Need for This Technology
Addressing complex problems across various fields often involves navigating vast parameter spaces. Examples include:
- Materials Science: Identifying optimal materials for advanced applications such as fusion confinement, battery electrodes, or solar cells.
- Logistics: Enhancing fuel efficiency and optimizing the transportation of goods, including solving challenges like the traveling salesman problem and improving airline travel.
- Security: Ensuring safe communication, implementing unbreakable data encryption, and enabling quantum key distribution.
- Finance: Optimizing financial portfolios and managing risk with precision.
Classical computing is not suitable for some of the world’s most sophisticated problems – this is where quantum computing steps in. With AtomQ technology, we aim to produce atomically defined and identical qubits - at scale - allowing us to achieve a fully scalable atomic quantum computer in order to appropriately address and tackle these diverse and complex problems.
Competition
Competing technologies in the quantum computing landscape include:
- Superconducting Circuitry: Utilizes superconducting materials to create qubits with high coherence times and fast gate speeds.
- Optically Trapped Neutral Atoms: Employs laser fields to trap and manipulate neutral atoms, enabling quantum computation with high fidelity.
- Electrostatically Trapped Ions: Uses electromagnetic fields to confine and control ions, facilitating precise quantum operations and error correction.
- Silicon T-Centres: Leverages defect centers in silicon for quantum information processing, offering potential for integration with existing silicon-based technologies.
These technologies represent the forefront of quantum computing advancements, each with its own strengths and challenges.
Key Innovation
AtomQ’s key innovation is deterministic creation of identical atomic quantum defects in the solid state at scale. No other approach in creation of qubits - the fundamental building block of a quantum computer - is both truly atomic and compatible with silicon technologies. Due to the precision and control of the distribution of electrons in aberration corrected electron microscopes, AtomQ is able to precisely deliver electrons in space and time, allowing to build identical structures atom by atom. For these reasons, we believe AtomQ is the first of its kind to have the potential to build truly scalable quantum computers.
R&D Status of Product
AtomQ is currently in the prototyping phase, undergoing optical evaluation, and integration into semiconducting and photonic circuitry.
Team Overview
- Kevin Roccapriore – Co-founder and President
ORNL PI
- Travis Humble – Director, Quantum Science Center, Computing and Computational Sciences Directorate
- Andrew Lupini – Group Leader, Scanning Transmission Electron Microscope, Physical Sciences Directorate

Nicholas Sokol
Algaeo
Nicholas Sokol is the founder and CEO of Algaeo. Nicholas has a background in geography and atmospheric science and has worked across forecasting and in-situ observation and experimentation. He has…

Nicholas Sokol
Algaeo
Nicholas Sokol is the founder and CEO of Algaeo. Nicholas has a background in geography and atmospheric science and has worked across forecasting and in-situ observation and experimentation. He has experience in energy, carbon capture, computational and data science, and agricultural sciences. He has worked for nonprofit and for-profit organizations. Passionate about environmental science and clean tech, Nicholas hopes to bring automation and efficiency increases to the agricultural sector with his technology while providing gigaton-scale absorption of carbon dioxide and increasing efficiency for farmers in the United States.
Project Abstract
Algaeo makes hardware that allows farmers to grow sustainable, efficient, and organic fertilizers on site using micro-algae and artificial intelligence. The company’s technology leverages adsorption to efficiently pull carbon dioxide and nitrogen from the atmosphere to feed algae. Algaeo uses three nontoxic algal strains, which are are scientifically proven to benefit soil health and boost plant growth by providing nutrients, to capture carbon from the atmosphere. Algaeo reduces farmer costs for fertilizer, improves yield and quality, and improves soil health for future growing seasons.
We Are Looking For
To be the "Everything Algae Company":
- Products and Services: Biofertilizers, Biostimulants, Biochar, Algae-Based Materials, and Environmental Services.
- Technologies: Hardware that enhances algae growth and monitors carbon capture.
- Focus: Agriculture-centric solutions aimed at helping farmers and gardeners increase yield, reduce costs, and automate on-site processes.
Critical Need for This Technology
Algaeo addresses the challenges faced by farmers and gardeners by using microalgae and microbes to enhance crop yield while lowering costs. Synthetic fertilizers, which often lead to significant emissions, nutrient leaching into waterways, and harmful environmental effects, also present financial challenges due to their variable costs. Algaeo provides a sustainable solution by offering a product that captures carbon, reduces nutrient leaching, and improves soil health, thereby boosting crop production. Their technology is essential for fostering a sustainable environment and advancing the circular economy through the effective use of microalgae.
Key Innovation
Algaeo offers advanced hardware that enables farmers and gardeners to produce sustainable, organic biofertilizers and biostimulants directly on site. Our technology features a unique blend of microbes designed to enhance crop growth and utilizes a sophisticated hardware system to efficiently capture carbon dioxide and nitrogen from the atmosphere, fostering optimal microbial growth in a controlled environment.
R&D Status of Product
Experimental development stage: We are actively working with different materials and processes to make our product more efficient.
Team Overview
- Nicholas Sokol – Co-Founder and Chief Executive Officer
- Anthony Sanguinetti – Business Development and Finance
ORNL PI
- Kuntal De – Technical Professional, Plant Systems Biology, Biological and Environmental Systems Sciences Directorate
Nicholas Sokol is the founder and CEO of Algaeo. Nicholas has a background in geography and atmospheric science and has worked across forecasting and in-situ observation and experimentation. He has experience in energy, carbon capture, computational and data science, and agricultural sciences. He has worked for nonprofit and for-profit organizations. Passionate about environmental science and clean tech, Nicholas hopes to bring automation and efficiency increases to the agricultural sector with his technology while providing gigaton-scale absorption of carbon dioxide and increasing efficiency for farmers in the United States.
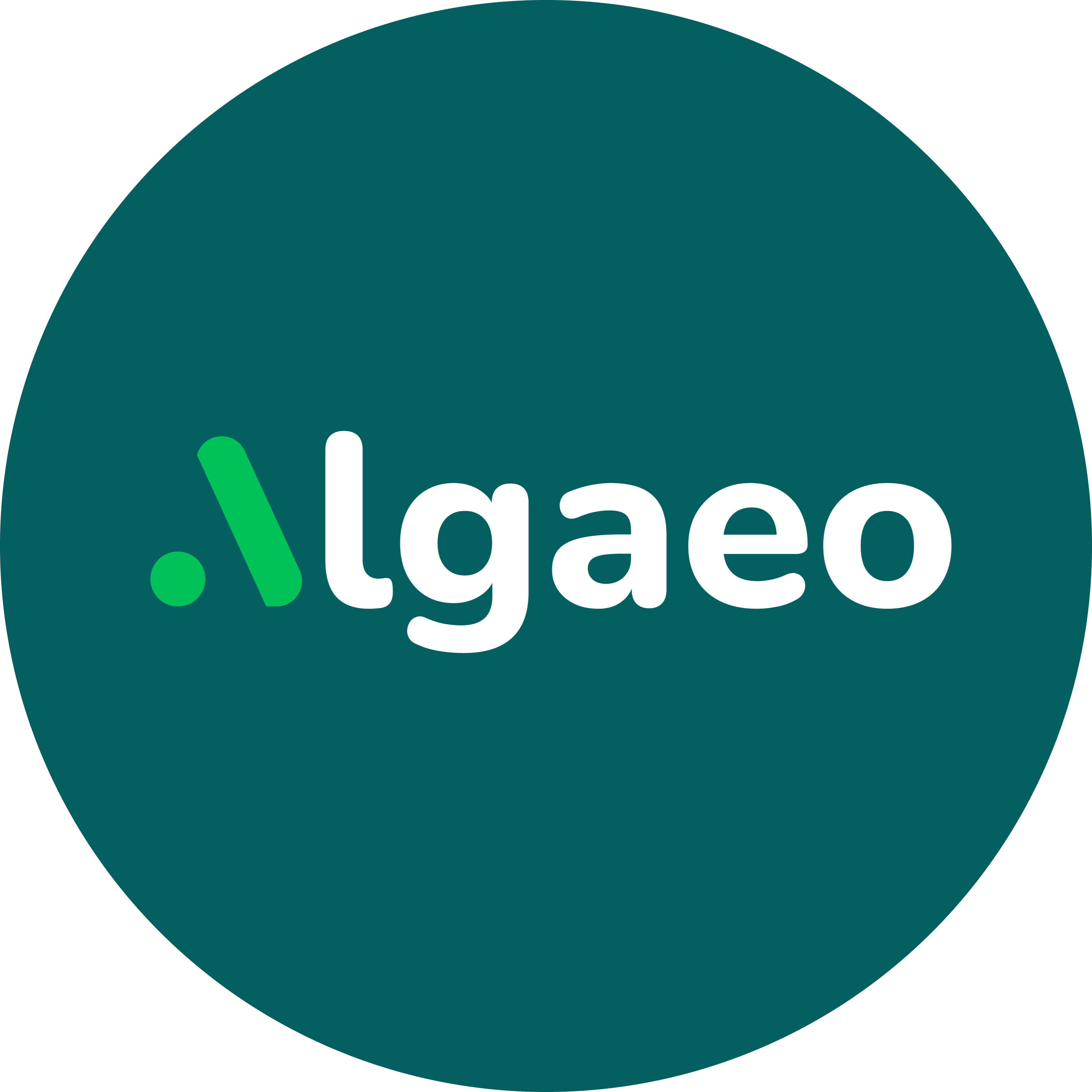
Project Abstract
Algaeo makes hardware that allows farmers to grow sustainable, efficient, and organic fertilizers on site using micro-algae and artificial intelligence. The company’s technology leverages adsorption to efficiently pull carbon dioxide and nitrogen from the atmosphere to feed algae. Algaeo uses three nontoxic algal strains, which are are scientifically proven to benefit soil health and boost plant growth by providing nutrients, to capture carbon from the atmosphere. Algaeo reduces farmer costs for fertilizer, improves yield and quality, and improves soil health for future growing seasons.
We Are Looking For
To be the "Everything Algae Company":
- Products and Services: Biofertilizers, Biostimulants, Biochar, Algae-Based Materials, and Environmental Services.
- Technologies: Hardware that enhances algae growth and monitors carbon capture.
- Focus: Agriculture-centric solutions aimed at helping farmers and gardeners increase yield, reduce costs, and automate on-site processes.
Critical Need for This Technology
Algaeo addresses the challenges faced by farmers and gardeners by using microalgae and microbes to enhance crop yield while lowering costs. Synthetic fertilizers, which often lead to significant emissions, nutrient leaching into waterways, and harmful environmental effects, also present financial challenges due to their variable costs. Algaeo provides a sustainable solution by offering a product that captures carbon, reduces nutrient leaching, and improves soil health, thereby boosting crop production. Their technology is essential for fostering a sustainable environment and advancing the circular economy through the effective use of microalgae.
Key Innovation
Algaeo offers advanced hardware that enables farmers and gardeners to produce sustainable, organic biofertilizers and biostimulants directly on site. Our technology features a unique blend of microbes designed to enhance crop growth and utilizes a sophisticated hardware system to efficiently capture carbon dioxide and nitrogen from the atmosphere, fostering optimal microbial growth in a controlled environment.
R&D Status of Product
Experimental development stage: We are actively working with different materials and processes to make our product more efficient.
Team Overview
- Nicholas Sokol – Co-Founder and Chief Executive Officer
- Anthony Sanguinetti – Business Development and Finance
ORNL PI
- Kuntal De – Technical Professional, Plant Systems Biology, Biological and Environmental Systems Sciences Directorate
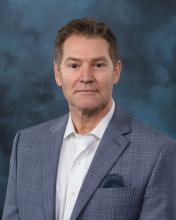
Tim Vosburgh
Coulomb Technology
Tim Vosburgh is the founder and CEO of Coulomb Technology, headquartered in Meridian, Idaho. With nearly thirty years of experience in electronics and contract manufacturing, Tim is a seasoned…
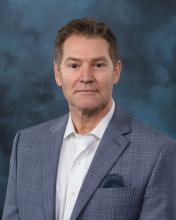
Tim Vosburgh
Coulomb Technology
Tim Vosburgh is the founder and CEO of Coulomb Technology, headquartered in Meridian, Idaho. With nearly thirty years of experience in electronics and contract manufacturing, Tim is a seasoned industry veteran. He has a proven track record of entrepreneurship in advanced battery technologies.
Project Abstract
Coulomb Technology is pioneering the development of revolutionary battery cells aimed at transforming the energy storage, backup power, and e-mobility sectors. Their innovative technology leverages zinc, manganese dioxide, and seawater, offering a safer and more sustainable alternative to traditional lithium batteries. Coulomb's batteries are not only designed to be faster charging but also come at half the cost of current lithium-ion solutions, addressing the pressing need for cost-effective energy storage.
A standout feature of Coulomb’s technology is its patent-pending 3D-electroplated anode. This advanced design effectively mitigates issues such as dendrite formation and corrosion, which are common challenges in battery performance. Additionally, the anode is engineered to function efficiently in low pH environments, further enhancing the battery’s versatility and durability.
Coulomb Technology’s batteries are built to meet the increasing demand for high-performance energy solutions while utilizing abundant, environmentally friendly materials. This innovation positions Coulomb as a leader in advancing battery technology, with the potential to significantly impact the energy storage and electric mobility markets.
Critical Need for This Technology
Climate change presents an urgent global challenge, and effective energy storage is a key component of addressing it. Many current battery technologies face significant issues, including high costs, safety risks, and reliance on scarce materials. Coulomb Technology’s innovative batteries are designed to overcome these challenges by offering a safer, more affordable, and environmentally friendly alternative.
Our batteries are specifically engineered to enhance the affordability and efficiency of intermittent renewable energy sources, such as wind and solar power. By reducing the costs and improving the safety of energy storage, we aim to make these sustainable energy sources more viable and widely adopted.
Additionally, we are targeting e-mobility markets including e-bikes, golf carts, and vehicle starter batteries. Existing lithium-ion solutions are plagued by safety and cost concerns, while lead-acid batteries suffer from short cycle life. Coulomb’s technology addresses these issues, providing a more durable and cost-effective solution for various applications in the e-mobility sector.
Competition
While there are other companies in the zinc-ion battery space, such as Urban Electric Power, Enerpoly, and Salient, our technology offers significant advantages. Compared to these competitors, our batteries have approximately 33% higher energy density, are priced at about half of their target cost, and deliver a cycle life that is twice as long.
Key Innovation
Our key innovation is an acidic zinc-ion battery that enhances energy density by leveraging the second electron of MnO₂. Additionally, we have developed a 3D electroplated anode that significantly reduces dendrite formation, improving battery performance and longevity.
R&D Status of Product
We are currently at TRL 4, with a dedicated team of three working full-time in the lab to optimize our battery technology. Our current focus is on 0.7Ah pouch cells, with optimization expected to be completed by October 2024. Following this, we plan to scale up to 5Ah pouch cells and subsequently to larger prismatic cells.
Team Overview
- Tim Vosburgh – Chief Executive Officer
- Allen Charkey – Chief Technology Officer
- Siyuan Gao – Senior Chemist
- Matt Gilmurray – Anode Scientist
- Matthew Kim – Senior Chemist
- Suqi Li – Cathode Scientist
ORNL PI
- Ilias Belharouak – Section Head, Electrification and Energy Infrastructure, Energy Science and Technology Directorate
- Parans Paranthaman – Group Member, Nanomaterials Chemistry, Physical Sciences Directorate
Tim Vosburgh is the founder and CEO of Coulomb Technology, headquartered in Meridian, Idaho. With nearly thirty years of experience in electronics and contract manufacturing, Tim is a seasoned industry veteran. He has a proven track record of entrepreneurship in advanced battery technologies.
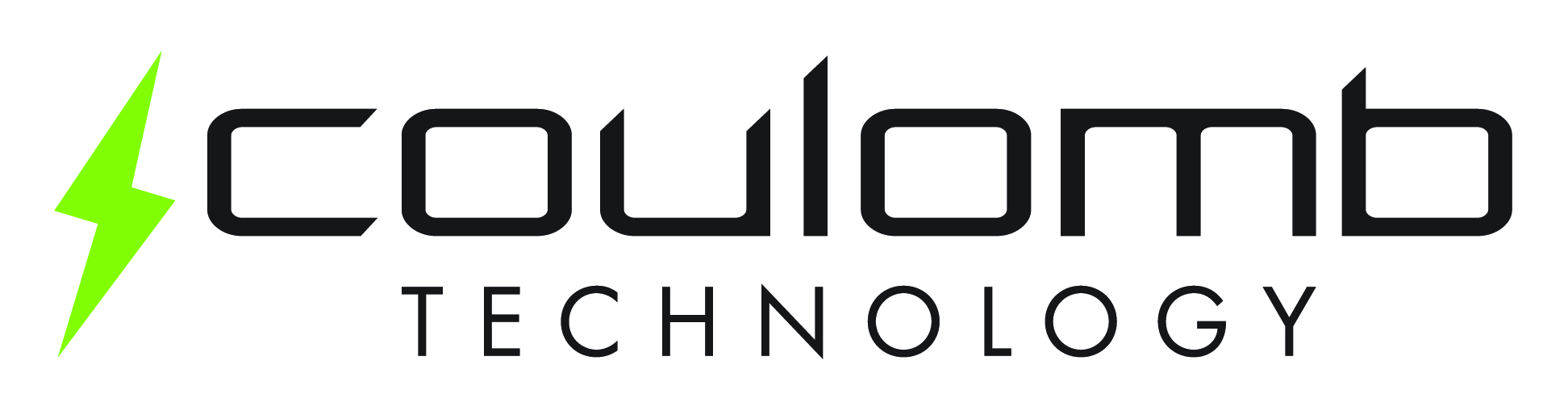
Project Abstract
Coulomb Technology is pioneering the development of revolutionary battery cells aimed at transforming the energy storage, backup power, and e-mobility sectors. Their innovative technology leverages zinc, manganese dioxide, and seawater, offering a safer and more sustainable alternative to traditional lithium batteries. Coulomb's batteries are not only designed to be faster charging but also come at half the cost of current lithium-ion solutions, addressing the pressing need for cost-effective energy storage.
A standout feature of Coulomb’s technology is its patent-pending 3D-electroplated anode. This advanced design effectively mitigates issues such as dendrite formation and corrosion, which are common challenges in battery performance. Additionally, the anode is engineered to function efficiently in low pH environments, further enhancing the battery’s versatility and durability.
Coulomb Technology’s batteries are built to meet the increasing demand for high-performance energy solutions while utilizing abundant, environmentally friendly materials. This innovation positions Coulomb as a leader in advancing battery technology, with the potential to significantly impact the energy storage and electric mobility markets.
Critical Need for This Technology
Climate change presents an urgent global challenge, and effective energy storage is a key component of addressing it. Many current battery technologies face significant issues, including high costs, safety risks, and reliance on scarce materials. Coulomb Technology’s innovative batteries are designed to overcome these challenges by offering a safer, more affordable, and environmentally friendly alternative.
Our batteries are specifically engineered to enhance the affordability and efficiency of intermittent renewable energy sources, such as wind and solar power. By reducing the costs and improving the safety of energy storage, we aim to make these sustainable energy sources more viable and widely adopted.
Additionally, we are targeting e-mobility markets including e-bikes, golf carts, and vehicle starter batteries. Existing lithium-ion solutions are plagued by safety and cost concerns, while lead-acid batteries suffer from short cycle life. Coulomb’s technology addresses these issues, providing a more durable and cost-effective solution for various applications in the e-mobility sector.
Competition
While there are other companies in the zinc-ion battery space, such as Urban Electric Power, Enerpoly, and Salient, our technology offers significant advantages. Compared to these competitors, our batteries have approximately 33% higher energy density, are priced at about half of their target cost, and deliver a cycle life that is twice as long.
Key Innovation
Our key innovation is an acidic zinc-ion battery that enhances energy density by leveraging the second electron of MnO₂. Additionally, we have developed a 3D electroplated anode that significantly reduces dendrite formation, improving battery performance and longevity.
R&D Status of Product
We are currently at TRL 4, with a dedicated team of three working full-time in the lab to optimize our battery technology. Our current focus is on 0.7Ah pouch cells, with optimization expected to be completed by October 2024. Following this, we plan to scale up to 5Ah pouch cells and subsequently to larger prismatic cells.
Team Overview
- Tim Vosburgh – Chief Executive Officer
- Allen Charkey – Chief Technology Officer
- Siyuan Gao – Senior Chemist
- Matt Gilmurray – Anode Scientist
- Matthew Kim – Senior Chemist
- Suqi Li – Cathode Scientist
ORNL PI
- Ilias Belharouak – Section Head, Electrification and Energy Infrastructure, Energy Science and Technology Directorate
- Parans Paranthaman – Group Member, Nanomaterials Chemistry, Physical Sciences Directorate